Introduction
Enterprise Resource Planning (ERP) systems are the backbone of modern business operations, integrating processes and data across departments into a unified platform. For manufacturing and industrial automation, ERP is a critical enabler of efficiency, scalability, and innovation. This post will explore ERP systems through the lens of manufacturing, offering technical decision-makers comprehensive insights to inform strategy and execution.
Definition of ERP
ERP, or Enterprise Resource Planning, is a category of software that integrates core business functions into a single, cohesive system. These functions often include:
- Finance and Accounting: Budgeting, forecasting, and financial reporting.
- Human Resources (HR): Payroll, employee records, and talent management.
- Inventory and Supply Chain Management: Procurement, inventory tracking, and logistics.
- Manufacturing and Operations: Production planning, quality control, and maintenance.
- Customer Relationship Management (CRM): Sales tracking, customer service, and order management.
At its core, ERP acts as a centralized hub, ensuring that data flows seamlessly between departments. By doing so, it eliminates silos, reduces redundancy, and enhances decision-making with real-time, accurate information.
Importance of ERP in Manufacturing and Industrial Automation
Manufacturing is a complex ecosystem requiring tight coordination between people, processes, and technology. ERP systems address this complexity by:
- Streamlining Operations: ERP integrates diverse activities such as production planning, inventory management, and quality control. This ensures that every department works toward shared goals, enhancing productivity and reducing waste.
- Providing Real-Time Data: Manufacturers operate in environments where timely decisions are critical. ERP systems offer real-time visibility into production schedules, resource utilization, and supply chain status.
- Facilitating IT-OT Convergence: In industrial automation, ERP bridges Information Technology (IT) and Operational Technology (OT) systems. It connects high-level planning tools with shop-floor control systems like SCADA, MES, and PLCs.
- Supporting Compliance and Quality: Manufacturing sectors, especially in regulated industries like food, pharmaceuticals, and automotive, rely on ERP for compliance management. It helps maintain audit trails, document control, and traceability.
- Enabling Scalability: As manufacturers expand, ERP systems adapt to increased complexity, supporting multi-location operations and global supply chains.
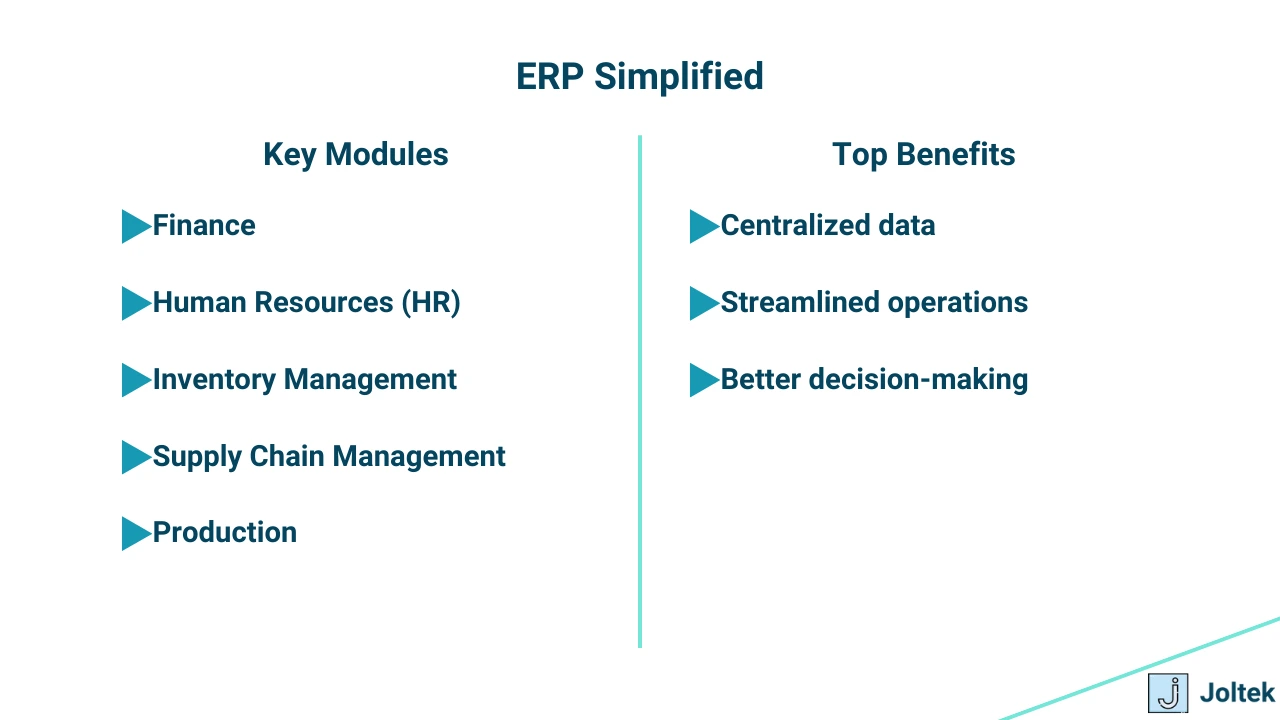
Goals of the Post
The purpose of this post is threefold:
- Educate Technical Decision-Makers: By offering a clear understanding of ERP fundamentals and their application in manufacturing, this post equips decision-makers to evaluate and implement these systems effectively.
- Highlight the ERP Ecosystem: From integrations with MES and SCADA to insights into ERP vendors, deployment strategies, and stakeholder roles, the post covers every angle of ERP in manufacturing.
- Provide Actionable Insights: Decision-makers will gain practical guidance on ERP selection, deployment, and maximizing ROI, supported by real-world examples and statistics.
This post aims to be your go-to resource for navigating the complex yet rewarding journey of ERP implementation in manufacturing and industrial automation. Let's dive deeper into the fundamentals of ERP to set the stage.
Fundamentals of ERP
Understanding ERP begins with its foundational concepts, which encompass its definition, core functionalities, historical evolution, and the transformative benefits it brings to organizations. This section lays the groundwork for comprehending ERP’s critical role in manufacturing and industrial automation.
What is ERP?
ERP, or Enterprise Resource Planning, is a comprehensive software system designed to manage and integrate an organization’s core business processes. It provides a centralized platform where different departments—such as finance, human resources, production, and procurement—can share information and collaborate efficiently.
ERP systems are built on a shared database and standardized processes, ensuring that data entered in one area becomes accessible across the organization in real time. This eliminates data silos, reduces redundancy, and improves overall operational efficiency.
Core Modules of ERP
ERP systems are modular in nature, meaning they offer a suite of functionalities that organizations can adopt based on their needs. Key modules include:
- Finance and Accounting: Handles budgeting, financial reporting, accounts payable/receivable, and compliance.
- Human Resources (HR): Manages payroll, employee records, recruitment, training, and performance evaluation.
- Inventory Management: Tracks raw materials, work-in-progress, and finished goods, ensuring optimal stock levels.
- Supply Chain Management: Coordinates procurement, vendor management, logistics, and demand forecasting.
- Production and Manufacturing: Oversees production planning, scheduling, quality control, and maintenance.
- Customer Relationship Management (CRM): Focuses on sales, marketing, customer service, and order management.
- Procurement: Automates purchase orders, supplier evaluations, and contract management.
- Business Intelligence (BI): Provides advanced analytics and reporting for informed decision-making.
Integration Capabilities
Modern ERP systems excel in integrating with external and internal systems, ensuring seamless data exchange. Key integration features include:
- Horizontal Integration: ERP connects departments such as finance, procurement, and HR under a single system.
- Vertical Integration: ERP interfaces with operational technologies like MES, SCADA, and PLCs, bridging the gap between the shop floor and enterprise management.
- Third-Party Integration: Many ERP systems offer APIs for connecting with specialized software like CAD tools, warehouse management systems, and IoT platforms.
Integration ensures that manufacturers can maintain a unified digital thread, enabling real-time visibility and control across the enterprise.
History and Evolution
ERP systems have evolved over decades, mirroring advancements in technology and business practices:
- Material Requirements Planning (MRP) – 1960s:
- Early systems focused on inventory management and production planning.
- MRP was limited to manufacturing operations and lacked broader organizational integration.
- MRP II (Manufacturing Resource Planning) – 1970s and 1980s:
- Expanded MRP by including financial and operational planning.
- Enhanced capabilities to synchronize production with business strategies.
- Emergence of ERP – 1990s:
- The term ERP was coined as systems integrated more functions, including HR, CRM, and supply chain management.
- Relational databases and client-server architectures fueled this evolution.
- Modern ERP – 2000s to Present:
- Cloud-based ERP emerged, offering scalability, accessibility, and lower upfront costs.
- Advanced analytics, IoT, and AI integrations became standard, enabling predictive insights and automation.
Why ERP Matters
ERP systems are transformative because they address fundamental business challenges and unlock strategic opportunities.
1. Centralized Data
ERP eliminates the inefficiencies of disconnected systems by centralizing data. This ensures that all departments operate from a single source of truth, reducing errors and improving collaboration. For example:
- A production delay detected in the manufacturing module automatically alerts procurement to adjust supply schedules.
2. Streamlined Operations
By standardizing processes and automating routine tasks, ERP systems enhance operational efficiency. Key benefits include:
- Faster order processing through integrated inventory and sales modules.
- Reduced downtime via proactive maintenance scheduling.
3. Improved Decision-Making
ERP provides real-time insights through robust reporting and analytics. Decision-makers can:
- Analyze trends in production output, costs, and quality metrics.
- Simulate “what-if” scenarios to anticipate and plan for future needs.
ERP is more than just a tool; it’s a strategic enabler for organizations seeking to thrive in today’s competitive and technology-driven landscape. In the next section, we’ll explore how ERP interacts with other manufacturing solutions like MES, SCADA, and PLCs, bridging enterprise-level planning with shop-floor execution.
ERP and Manufacturing Solutions
In manufacturing and industrial automation, ERP systems play a vital role in managing enterprise-level planning and resource allocation. However, their full potential is unlocked when integrated with manufacturing-specific systems like MES, SCADA, PLCs, and HMIs. This section delves into the relationships between these systems and highlights how ERP systems enable streamlined and efficient manufacturing operations.
ERP vs. MES (Manufacturing Execution Systems)
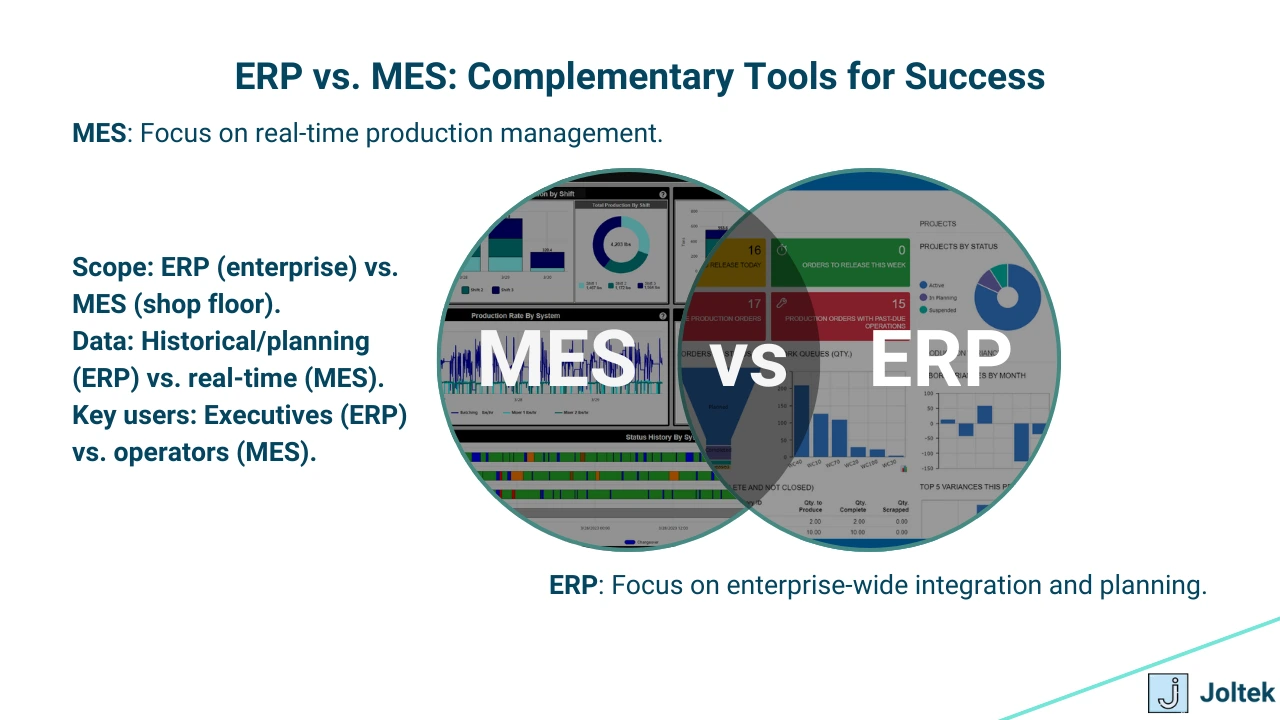
Definitions and Scope
- ERP (Enterprise Resource Planning):
- Focuses on enterprise-level resource management.
- Covers financial planning, supply chain management, inventory, and high-level production planning.
- Oriented toward the business layer of an organization.
- MES (Manufacturing Execution System):
- Operates at the manufacturing layer, managing real-time production processes.
- Tracks production schedules, machine performance, material usage, and quality.
- Provides visibility into shop-floor operations, ensuring optimal efficiency.
Complementary Roles
- ERP and MES are not competitors but partners in achieving manufacturing excellence.
- ERP handles planning and resource allocation, while MES ensures execution aligns with the plan.
- Together, they enable closed-loop manufacturing, where decisions made at the enterprise level are continuously informed by real-time shop-floor data.
Integrating ERP with SCADA, PLC, and HMI
How ERP Connects with Lower-Level Automation Systems
ERP systems connect to shop-floor technologies through middleware platforms, APIs, or Unified Namespace (UNS) architectures. Here's how these connections function:
- SCADA (Supervisory Control and Data Acquisition): Monitors and controls plant operations. Data from SCADA systems is aggregated and sent to ERP for analytics and planning.
- PLCs (Programmable Logic Controllers): Perform real-time machine control. ERP uses aggregated data from PLCs (via MES or SCADA) for production tracking and maintenance scheduling.
- HMIs (Human-Machine Interfaces): Allow operators to interact with machines. Insights from HMI data flow upward into ERP for visibility into shop-floor conditions.
Benefits of Vertical Integration
Vertical integration bridges the gap between enterprise systems (ERP) and operational technologies (OT), enabling:
- Real-Time Visibility: ERP provides real-time dashboards showing production status, delays, and resource utilization.
- Proactive Maintenance: Data from PLCs is analyzed to predict equipment failures, minimizing downtime.
- Optimized Production: Integration enables dynamic scheduling adjustments based on real-time shop-floor conditions.
- Improved Compliance: Centralized reporting ensures traceability, critical for regulated industries.
Case Studies
Case Study 1: Automotive Manufacturer – ERP and MES Integration
Challenge: An automotive manufacturer struggled with mismatches between production schedules in ERP and shop-floor realities. Delays were frequent, leading to missed delivery deadlines.
Solution:
- Integrated SAP ERP with a Siemens MES system.
- ERP handled material planning and procurement, while MES provided real-time production updates.
- Data synchronization allowed dynamic rescheduling when delays occurred.
Outcome:
- Production efficiency improved by 20%.
- Delivery timelines were consistently met.
Case Study 2: Food & Beverage Company – ERP with SCADA
Challenge: A food processing plant faced issues with batch traceability and quality control due to disconnected systems.
Solution:
- Implemented an Oracle ERP integrated with Wonderware SCADA.
- ERP managed recipe planning and compliance documentation.
- SCADA provided real-time data on batch processing and machine parameters, feeding it into ERP for audit trails.
Outcome:
- Achieved full traceability of ingredients and batches.
- Reduced quality incidents by 15%.
Case Study 3: Pharmaceutical Company – ERP with PLCs
Challenge: A pharmaceutical facility lacked visibility into production downtime caused by machine failures.
Solution:
- Integrated Microsoft Dynamics ERP with Rockwell Automation PLCs.
- PLCs provided detailed data on machine health, which ERP used to generate maintenance alerts.
Outcome:
- Equipment downtime decreased by 25%.
- Maintenance costs were optimized by focusing on preventive rather than reactive repairs.
By integrating ERP with MES, SCADA, PLC, and HMI systems, manufacturers create a cohesive digital thread that enhances operational efficiency, reduces costs, and improves product quality. The next section will explore how organizations can select and deploy ERP systems to maximize these benefits.
Selecting and Deploying ERP Systems
Implementing an ERP system is one of the most transformative decisions an organization can make. For manufacturers, the stakes are even higher as ERP systems not only integrate administrative processes but also connect with shop-floor technologies. Success depends on selecting the right system for your business and executing a carefully managed deployment process.
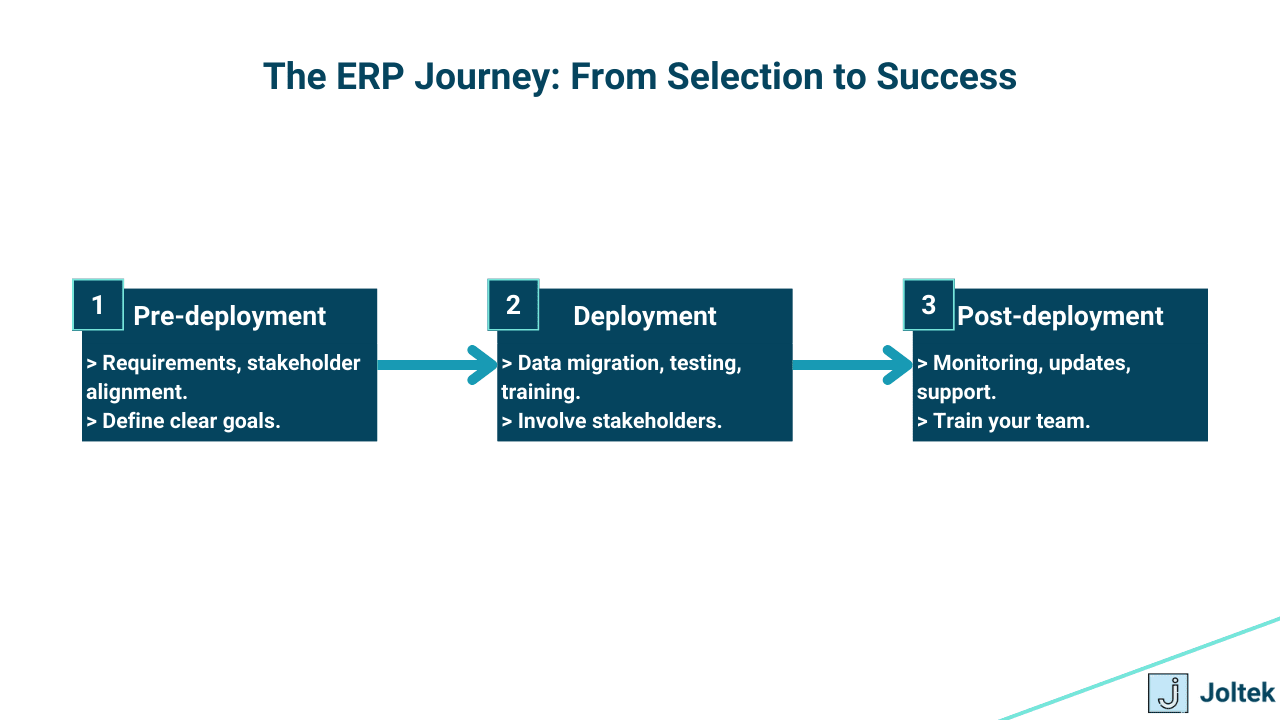
Factors to Consider
When selecting an ERP system, organizations must consider their size, industry needs, and desired level of customization. Smaller manufacturers often prioritize simplicity and cost-effectiveness, making cloud-based or modular ERP solutions appealing. These systems provide essential functionalities without overwhelming complexity, offering a scalable solution as the business grows. Larger enterprises, on the other hand, require ERP platforms capable of managing complex operations across multiple locations. For these organizations, robust features such as advanced analytics, multi-currency support, and deep customization are often critical.
Industry requirements also play a significant role in ERP selection. For example, process manufacturers in sectors like food and pharmaceuticals often demand ERP systems with strong capabilities for batch tracking, quality management, and regulatory compliance. By contrast, discrete manufacturers, such as those in automotive or electronics, might prioritize features for production scheduling, inventory optimization, and supply chain visibility. Understanding these industry-specific needs ensures that the chosen system aligns with both operational workflows and strategic goals.
Another critical decision is whether to opt for a highly customizable ERP or an off-the-shelf solution. Customization allows companies to tailor the software to their exact processes, but it often comes with higher costs and longer deployment times. Off-the-shelf solutions, while faster and more cost-effective, may require businesses to adapt their processes to fit the system’s capabilities. Striking the right balance between these options is key to ensuring a successful implementation.
ERP Deployment Models
The deployment model an organization chooses—on-premises, cloud-based, or hybrid—affects both the immediate implementation process and long-term system performance. On-premises ERP systems are hosted and managed within the organization’s own infrastructure. While this option provides greater control over data and allows extensive customization, it requires significant upfront investment in hardware and ongoing IT support.
Cloud-based ERP solutions, hosted on the vendor’s infrastructure and accessed via the internet, have gained popularity due to their flexibility and lower initial costs. These systems are particularly advantageous for small and medium-sized businesses, offering subscription-based pricing, automatic updates, and remote accessibility. However, reliance on cloud hosting raises concerns about data security and connectivity, especially for manufacturers operating in remote locations or highly regulated industries.
Hybrid models combine the strengths of on-premises and cloud systems. These allow businesses to maintain critical functions in-house while leveraging cloud capabilities for scalability and advanced features. This approach is often chosen by manufacturers transitioning from legacy systems, as it allows them to modernize incrementally without disrupting core operations.
Steps in ERP Deployment
ERP deployment is a multi-phase process that begins long before the software is installed. The pre-deployment phase is crucial for setting the project’s foundation. Organizations must gather detailed requirements, engage stakeholders from across departments, and evaluate vendors to ensure alignment with business goals. A lack of clarity at this stage can lead to misaligned expectations and costly adjustments later.
The deployment phase focuses on turning plans into reality. Data migration is often one of the most challenging tasks, as it involves cleansing, standardizing, and transferring data from legacy systems into the new ERP platform. Thorough testing at this stage is essential to identify and address any issues before the system goes live. Equally important is employee training, as the success of an ERP implementation depends on its adoption by end-users. Tailored training programs should address the specific needs of different roles, ensuring that employees are confident and capable when using the new system.
After the system is launched, post-deployment activities such as monitoring, updates, and support are critical to maintaining long-term success. Regular monitoring helps identify performance bottlenecks and user issues, while timely updates keep the system secure and aligned with evolving business needs. Establishing an ongoing support structure, either in-house or through the vendor, ensures that the ERP system continues to deliver value.
Challenges in ERP Deployment
Despite their transformative potential, ERP implementations are notoriously challenging. One common issue is scope creep, where unplanned additions to the project’s requirements lead to delays and cost overruns. Organizations can mitigate this by defining clear objectives and sticking to them throughout the implementation process. Resistance to change is another frequent hurdle, as employees accustomed to existing workflows may hesitate to adopt the new system. Proactive change management strategies, including open communication and visible leadership support, are essential to overcoming these concerns.
Data quality is another critical factor. Migrating inaccurate or incomplete data into the ERP system can undermine its reliability and utility. Conducting a thorough audit of existing data before migration helps ensure that the new system starts with a solid foundation. Finally, inadequate training can lead to underutilization of ERP capabilities, reducing the return on investment. Companies should allocate sufficient resources to comprehensive and ongoing training programs.
By addressing these challenges with careful planning and execution, manufacturers can ensure a successful ERP deployment that drives efficiency, scalability, and long-term growth. In the next section, we will examine leading ERP vendors and how to evaluate them based on your organization’s needs.
ERP Vendors: Pros and Cons
Choosing the right ERP vendor is critical to the success of your implementation. The market is populated with both major players offering broad capabilities and niche providers catering to specific industries. This section explores the strengths, limitations, and emerging trends among ERP vendors, helping manufacturers make informed decisions.
Major ERP Vendors
Several ERP vendors dominate the global market, each offering unique strengths and trade-offs. Below is an overview of the key players:
- SAP
- Features and Strengths:
- Comprehensive suite of tools for large enterprises.
- Industry-leading capabilities in supply chain and production planning.
- Strong integration options with MES and SCADA systems.
- Limitations:
- High implementation costs and complexity.
- Steep learning curve for users.
- Pricing Considerations: SAP's pricing is typically on the higher end, making it more suitable for large manufacturers with significant budgets.
- Features and Strengths:
- Oracle NetSuite
- Features and Strengths:
- Cloud-native ERP with scalability for growing businesses.
- Excellent financial and inventory management tools.
- Strong support for multi-location and multi-currency operations.
- Limitations:
- Customization options can be limited compared to on-premises solutions.
- Integration with legacy systems can pose challenges.
- Pricing Considerations: Subscription-based pricing makes it accessible for small to mid-sized businesses.
- Features and Strengths:
- Microsoft Dynamics 365
- Features and Strengths:
- Seamless integration with Microsoft Office and Azure.
- Flexible deployment options: cloud, on-premises, or hybrid.
- User-friendly interface with robust analytics capabilities.
- Limitations:
- May require third-party tools for advanced manufacturing needs.
- Limited functionality for process manufacturing industries.
- Pricing Considerations: Offers competitive pricing with modular options for specific business needs.
- Features and Strengths:
- Infor
- Features and Strengths:
- Tailored solutions for manufacturing, particularly in aerospace, automotive, and food & beverage.
- Strong analytics and AI-driven tools.
- Limitations:
- Limited third-party integration compared to larger players.
- User experience can vary across modules.
- Pricing Considerations: Generally mid-range pricing, with a focus on specific industries.
- Features and Strengths:
- Epicor
- Features and Strengths:
- Designed specifically for small to medium-sized manufacturers.
- Strong capabilities in production planning, scheduling, and inventory management.
- Flexible customization options.
- Limitations:
- Limited scalability for very large enterprises.
- Less robust ecosystem for third-party integrations.
- Pricing Considerations: More affordable compared to larger players, making it ideal for mid-market manufacturers.
- Features and Strengths:
Niche and Industry-Specific ERP Providers
While major vendors offer broad functionality, niche ERP providers focus on specific industries or operational needs. These systems often excel in addressing unique challenges faced by manufacturers in specialized sectors.
- IQMS (Acquired by Dassault Systèmes):
- Tailored for discrete and process manufacturing.
- Strong capabilities in production monitoring and quality control.
- Limited scalability for very large enterprises.
- Plex Systems:
- Focuses on cloud-native ERP for manufacturing.
- Offers strong shop-floor integration and real-time production monitoring.
- Can lack advanced financial and HR features compared to larger platforms.
- Deacom:
- Designed for batch and process manufacturers.
- Features comprehensive compliance and traceability tools.
- May lack the flexibility and integrations of larger systems.
Niche providers are often a great choice for manufacturers with unique requirements but may be less versatile for organizations with broader needs or plans for diversification.
Emerging Trends in ERP
ERP systems continue to evolve, driven by technological advancements and changing business demands. Some key trends shaping the ERP landscape include:
- AI and Analytics Integration:
- Modern ERP systems increasingly leverage artificial intelligence (AI) for predictive analytics, automation, and decision-making support.
- Examples include demand forecasting, equipment failure prediction, and automated invoice processing.
- Industry-Specific ERP Modules:
- Vendors are offering pre-configured solutions tailored to specific industries, such as automotive, food and beverage, and pharmaceuticals.
- These modules reduce implementation time by addressing common pain points and compliance requirements out of the box.
- Cloud-First Strategies:
- Cloud-based ERP adoption continues to grow, particularly among small and medium-sized businesses. Vendors are investing in enhanced security, scalability, and multi-tenant architectures to support diverse users.
- IoT Integration:
- ERP systems are increasingly integrating IoT data to provide real-time insights into operations, enabling better monitoring and predictive maintenance.
- Sustainability and ESG Reporting:
- New ERP functionalities focus on helping organizations track and report on environmental, social, and governance (ESG) metrics to meet regulatory and market demands.
By understanding the strengths and limitations of ERP vendors and staying informed about emerging trends, manufacturers can align their ERP strategy with their long-term goals. The next section will explore the ecosystem of stakeholders involved in ERP implementation and how their collaboration drives success.
Stakeholders in the ERP Ecosystem
The success of an ERP implementation depends heavily on the involvement and alignment of various stakeholders. These stakeholders, both internal and external, play distinct roles in ensuring the system meets organizational goals while minimizing disruptions during deployment and beyond. Clear collaboration and communication among all parties are essential to achieve this alignment.
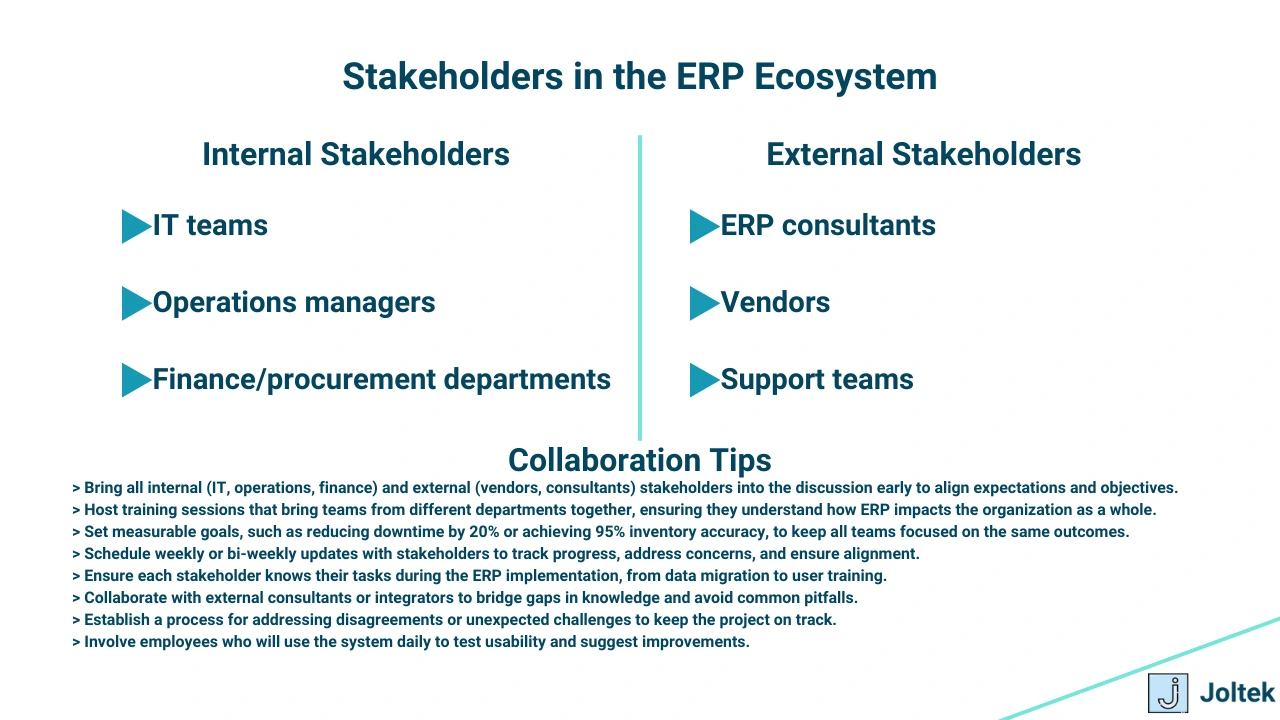
Internal Stakeholders
Internal stakeholders are individuals or teams within the organization who are directly involved in or affected by the ERP system. Their input and engagement are critical for understanding organizational needs and ensuring successful adoption.
- IT Teams
- The IT team is the backbone of ERP implementation, responsible for managing technical aspects such as infrastructure, system integration, and data migration.
- They play a key role in customizing the ERP system, troubleshooting technical issues, and ensuring cybersecurity measures are in place.
- Their collaboration with vendors and external consultants is crucial for smooth system integration with existing technologies, such as MES, SCADA, or legacy systems.
- Operations Managers
- Operations managers are critical in defining the functional requirements of the ERP system, particularly those related to production, inventory, and supply chain management.
- They act as a bridge between shop-floor realities and high-level enterprise planning, ensuring that the system supports operational efficiency.
- Their involvement during the testing phase ensures that workflows are optimized and user-specific challenges are addressed.
- Finance and Procurement Departments
- Finance teams rely on ERP systems for budgeting, financial reporting, and compliance. They ensure that the system provides accurate and timely insights into organizational performance.
- Procurement teams leverage ERP tools to streamline supplier management, monitor inventory levels, and optimize purchasing processes.
- Both departments are integral to the success of the ERP implementation, as financial oversight and resource management are key drivers of ROI.
External Stakeholders
External stakeholders bring specialized expertise and tools to facilitate the implementation process. Their involvement is particularly important for organizations lacking in-house resources or experience with ERP systems.
- ERP Consultants and Integrators
- Consultants provide guidance on selecting the right ERP system based on organizational goals, industry requirements, and budget constraints.
- Integrators focus on technical aspects, such as system configuration, data migration, and ensuring compatibility with existing technologies.
- Their experience with past implementations helps organizations avoid common pitfalls, such as scope creep or integration challenges.
- Vendors and Support Teams
- Vendors are responsible for providing the ERP software and offering technical support throughout its lifecycle.
- Their role often extends to offering training resources and best practices for deployment.
- Post-implementation, vendors continue to play a crucial role in delivering updates, addressing bugs, and ensuring system scalability as the business evolves.
Collaboration and Communication
The collaboration between internal and external stakeholders is the linchpin of a successful ERP project. Misalignment among these groups can lead to delays, inefficiencies, and unmet expectations. To ensure alignment, organizations should focus on the following strategies:
- Cross-Functional Teams: Establish a project team that includes representatives from all major departments—IT, operations, finance, and procurement. This ensures that diverse perspectives are considered throughout the project lifecycle.
- Clear Communication Channels: Regular meetings and progress updates foster transparency and allow stakeholders to address issues proactively. Leveraging project management tools can help keep everyone informed and on track.
- Defined Roles and Responsibilities: Clearly outline who is responsible for each phase of the ERP implementation, from requirements gathering to post-deployment support. This reduces confusion and ensures accountability.
- Stakeholder Alignment Workshops: Early-stage workshops can help align expectations, set priorities, and define success criteria for the ERP project. These workshops also build trust and foster collaboration among internal and external stakeholders.
- End-User Involvement: End-users—those who will interact with the ERP system daily—should be involved early in the process to provide feedback on usability and workflows. Their buy-in is critical to adoption.
By fostering collaboration among all stakeholders, organizations can streamline their ERP implementation process and maximize the system's benefits. Effective alignment ensures that technical expertise, operational needs, and strategic objectives are harmonized, resulting in a system that drives long-term value. In the next section, we will explore ERP’s role in digital transformation and its evolving trends in manufacturing.
ERP in the Context of Digital Transformation
In today’s rapidly evolving manufacturing landscape, ERP systems are pivotal to driving digital transformation. By serving as a central hub for data and process integration, ERPs enable organizations to leverage advanced technologies and respond swiftly to market demands. This section explores the role of ERP in Industry 4.0 and the trends shaping its evolution.
Role of ERP in Industry 4.0
Industry 4.0, often referred to as the Fourth Industrial Revolution, emphasizes the digitalization of manufacturing through smart technologies and interconnected systems. ERP systems are at the heart of this transformation, acting as the command center that integrates data from various sources and supports real-time decision-making.
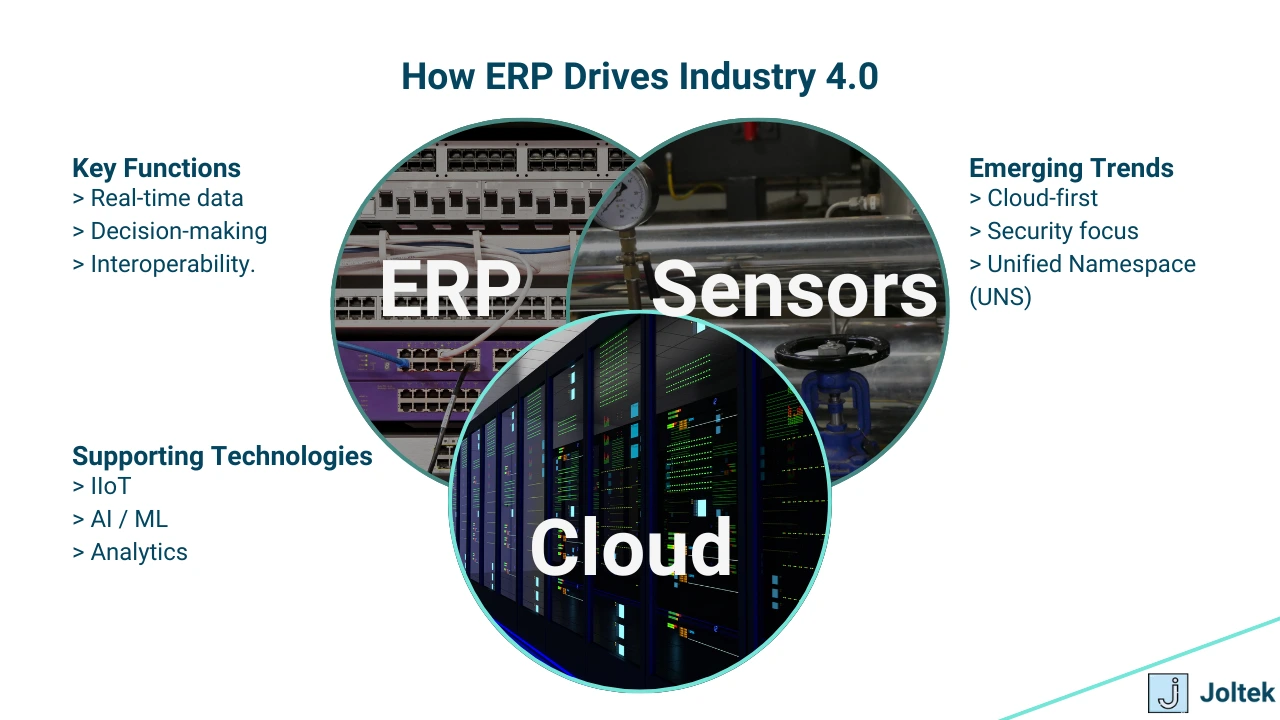
- Supporting Technologies: IoT, AI, and Analytics
ERP systems in Industry 4.0 are increasingly integrated with advanced technologies like the Internet of Things (IoT), Artificial Intelligence (AI), and analytics. These integrations enable manufacturers to:- IoT: Gather real-time data from sensors, machines, and production lines, feeding it directly into ERP systems for monitoring and optimization.
- AI: Enhance decision-making through predictive analytics, enabling activities such as demand forecasting, maintenance scheduling, and anomaly detection.
- Analytics: Provide actionable insights through dashboards and reports, helping organizations identify trends and optimize processes across operations.
- For example, a factory equipped with IoT-enabled machines can send performance data to an ERP system, which uses AI to predict equipment failures and recommend maintenance schedules, reducing downtime and costs.
- Real-Time Data and Decision-Making
Real-time data integration is a cornerstone of Industry 4.0, and ERP systems are designed to aggregate, process, and disseminate this data across the enterprise. Key benefits include:- Immediate visibility into inventory levels, production status, and supply chain disruptions.
- Faster response to customer demands and market changes, enabling just-in-time production and delivery.
- Improved collaboration between departments, as real-time data eliminates silos and fosters alignment.
- By connecting shop-floor technologies with high-level enterprise systems, ERP empowers manufacturers to operate with agility and precision in a competitive environment.
Trends Shaping ERP
As manufacturing continues to evolve, ERP systems are adapting to meet new challenges and opportunities. Several trends are driving this evolution:
- Cloud-First Strategies
The adoption of cloud-based ERP solutions is accelerating, driven by their flexibility, scalability, and lower upfront costs. Manufacturers are increasingly favoring cloud ERP for its:- Ease of deployment: Cloud systems eliminate the need for on-premises infrastructure, reducing implementation time.
- Scalability: Organizations can scale up or down based on changing needs without significant capital investment.
- Accessibility: Employees can access the ERP system from anywhere, enabling remote work and global operations.
- Gartner predicts that by 2026, more than 75% of midsize and large organizations will have moved to cloud ERP, underscoring the growing dominance of this model.
- Increased Focus on Security and Compliance
As ERP systems handle sensitive financial, operational, and customer data, security and compliance have become critical priorities. Manufacturers must address:- Cybersecurity threats: ERP systems are increasingly targeted by hackers, necessitating robust encryption, multi-factor authentication, and proactive monitoring.
- Regulatory compliance: Features such as automated audit trails and data retention policies help organizations meet industry-specific regulations, such as FDA requirements for pharmaceuticals or ISO standards for manufacturing.
- Vendors are responding by building advanced security features into ERP platforms and offering tools to simplify compliance reporting.
- Integration with Unified Namespace (UNS)
Unified Namespace (UNS) is an architecture that consolidates all plant data into a single, standardized platform, enabling seamless communication between devices and systems. ERP integration with UNS offers several advantages:- Enhanced interoperability: ERP systems can pull real-time data from MES, SCADA, and other operational technologies without complex integrations.
- Streamlined data management: UNS provides a single source of truth, simplifying data access and analysis for ERP systems.
- Improved scalability: Manufacturers can easily add new devices or systems to the architecture without disrupting existing ERP integrations.
- As UNS adoption grows, ERP systems that align with this architecture will be better positioned to support digital transformation efforts.
ERP systems are no longer just back-office tools; they are strategic enablers of Industry 4.0 and digital transformation. By integrating with IoT, AI, and analytics, ERP platforms help manufacturers achieve real-time decision-making and operational excellence. At the same time, trends like cloud-first strategies, heightened security focus, and Unified Namespace integration ensure that ERP systems remain adaptable and future-proof. In the next section, we will explore how organizations can measure the success of ERP implementations and learn from real-world examples.
Metrics and Success Stories
Evaluating the success of an ERP system goes beyond its deployment. To justify the investment and guide future improvements, organizations need to measure its return on investment (ROI) and learn from real-world examples. This section explores the key metrics for measuring ERP effectiveness and highlights success stories and lessons from manufacturing implementations.
Measuring ERP ROI
Quantifying the ROI of an ERP system involves analyzing its impact across various dimensions of organizational performance. For manufacturers, these metrics often include improvements in operational efficiency, reduced downtime, and increased productivity.
- Operational Efficiency
ERP systems streamline workflows and automate manual tasks, allowing teams to focus on value-added activities. Metrics to track include:- Inventory Turnover Ratio: Higher turnover rates indicate better inventory management and reduced holding costs.
- Order Fulfillment Cycle Time: ERP systems can shorten the time it takes to process, manufacture, and deliver customer orders.
- For example, a manufacturer that implemented an ERP with integrated inventory and production planning saw a 15% reduction in order processing time, translating to faster customer deliveries and higher satisfaction.
- Reduced Downtime
Through better maintenance planning and real-time monitoring, ERP systems help minimize equipment downtime. Key metrics include:- Mean Time Between Failures (MTBF): Tracking the average operational time between equipment failures.
- Unplanned Downtime Hours: Reduction in unscheduled stoppages directly impacts production capacity.
- A food processing company using IoT-enabled ERP reduced unplanned downtime by 20% by leveraging predictive maintenance alerts tied to sensor data.
- Increased Productivity
ERP systems provide a single source of truth, enabling teams to work more efficiently and make informed decisions. Metrics to assess productivity gains include:- Production Throughput: Measuring the output per unit of time.
- Employee Productivity: Evaluating improvements in performance per worker, driven by automation and better resource allocation.
- In one case, a mid-sized electronics manufacturer increased production throughput by 25% after implementing an ERP that streamlined workflow scheduling and eliminated redundant processes.
Case Studies
- Successful ERP Implementation: Automotive Supplier
- Challenge: A Tier-1 automotive supplier struggled with inefficient production scheduling and inventory management, leading to frequent stockouts and missed deadlines.
- Solution: Implemented SAP S/4HANA, integrating supply chain, production planning, and inventory management modules.
- Outcome: Achieved a 30% improvement in inventory accuracy, reduced production lead times by 25%, and consistently met delivery deadlines.
- Key Takeaway: Cross-departmental alignment during the requirements-gathering phase ensured the ERP system addressed critical pain points.
- Successful ERP Implementation: Pharmaceutical Manufacturer
- Challenge: A pharmaceutical company needed to comply with stringent FDA regulations, requiring robust batch tracking and documentation.
- Solution: Deployed Oracle NetSuite with built-in compliance tools and integrated it with MES for real-time production tracking.
- Outcome: Reduced compliance-related errors by 40%, improved batch traceability, and passed regulatory audits with minimal findings.
- Key Takeaway: Selecting an ERP system with industry-specific features ensured compliance and reduced manual documentation burdens.
- Lessons from ERP Failure: Aerospace Manufacturer
- Challenge: An aerospace company attempted to implement an overly customized ERP system without proper stakeholder involvement.
- Problem: The system faced frequent delays and cost overruns, with poor alignment between software capabilities and actual business needs.
- Outcome: Abandoned the project after investing millions, leading to operational disruptions and loss of customer trust.
- Key Takeaway: Over-customization and lack of user involvement can derail ERP projects. Phased implementation and stakeholder alignment are critical to success.
Measuring the ROI of an ERP system is essential to demonstrate its value and identify areas for optimization. Metrics such as operational efficiency, downtime reduction, and productivity gains offer quantifiable proof of success, while case studies provide practical insights into what works—and what doesn’t. By analyzing both successes and failures, manufacturers can refine their ERP strategies and ensure long-term benefits for their operations.
Conclusion
ERP systems are transformative tools that have reshaped the manufacturing landscape, enabling organizations to integrate their operations, enhance efficiency, and remain competitive in an increasingly complex environment. Through this post, we’ve explored the fundamentals of ERP, its integration with manufacturing systems, selection and deployment strategies, vendor insights, stakeholder roles, and its role in digital transformation. By understanding these elements, technical decision-makers can make informed choices about ERP systems that align with their organizational goals.
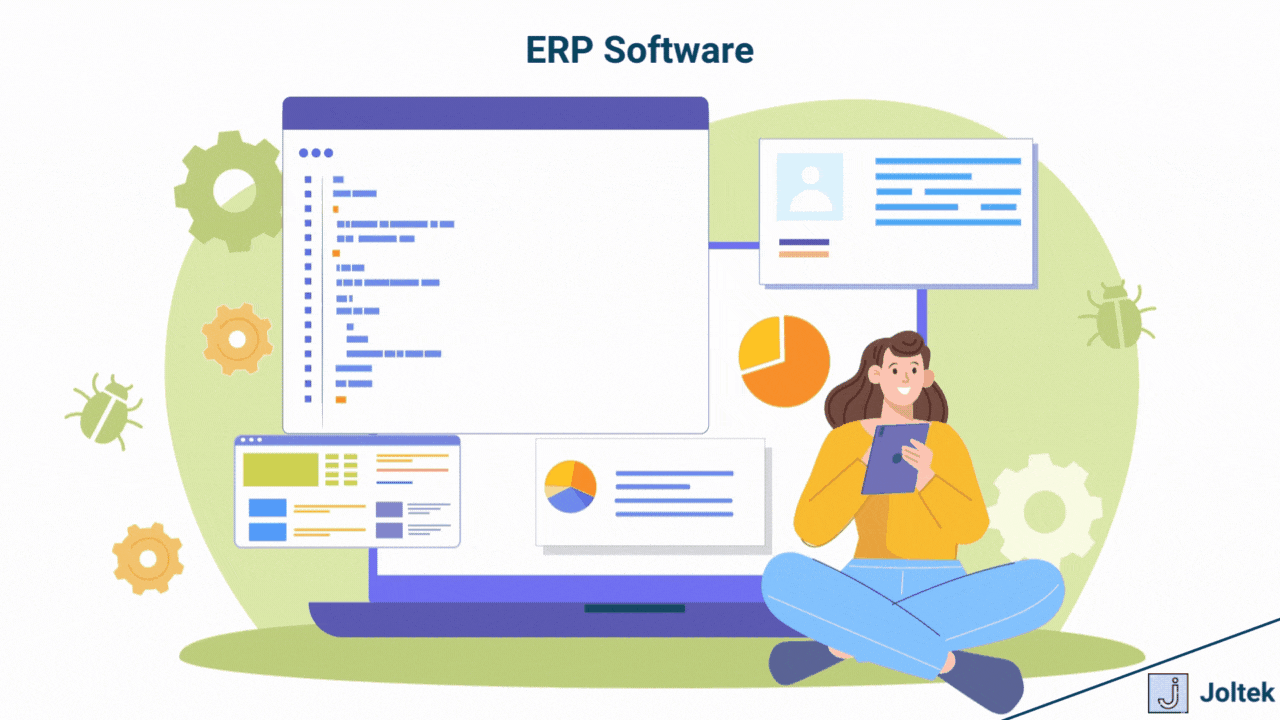
Summary of Key Points
- ERP Fundamentals: ERP systems consolidate core business functions into a single platform, offering centralized data management, streamlined operations, and improved decision-making.
- Integration with Manufacturing Solutions: ERP complements systems like MES, SCADA, and PLCs, creating a seamless flow of information between shop-floor technologies and enterprise-level planning.
- Selection and Deployment: Successful ERP projects depend on matching system capabilities to organizational needs, choosing the right deployment model, and following a structured implementation process.
- Vendor Landscape: Both major players and niche providers offer diverse ERP solutions, and selecting the right vendor involves balancing functionality, scalability, and cost considerations.
- Role in Digital Transformation: ERP systems are pivotal in Industry 4.0, integrating with IoT, AI, and analytics to enable real-time insights and operational agility.
- Measuring Success: Metrics like operational efficiency, downtime reduction, and productivity gains help quantify ERP ROI, while case studies provide actionable lessons.
Importance of Aligning ERP Strategy with Manufacturing Goals
The effectiveness of an ERP system hinges on its alignment with the unique needs and objectives of the organization. For manufacturers, this means ensuring that the system supports production efficiency, supply chain visibility, and regulatory compliance while adapting to future technological trends. ERP strategies should be driven by both operational priorities and long-term business goals, with input from all key stakeholders to ensure adoption and impact.
Next Steps for Readers
To get started with ERP implementation or optimization, consider the following steps:
- Evaluation: Assess your organization’s current processes, pain points, and future needs to identify gaps that an ERP system can address.
- Consultation: Engage with ERP consultants, integrators, or vendors to explore available options and align them with your business objectives.
- Planning: Develop a clear roadmap for ERP deployment, including timelines, resource allocation, and change management strategies. Ensure buy-in from internal stakeholders and set measurable success criteria.
ERP implementation is a significant investment, but when executed correctly, it can transform your manufacturing operations and provide a foundation for sustained growth. Take the time to evaluate your needs, collaborate with experts, and build a strategic plan that sets your organization up for success.