Introduction: From Planning to Execution
In the first article of this series, we explored the broader role of Manufacturing Execution Systems (MES) in modern factories — acting as the connective tissue between high-level business planning (ERP) and low-level machine control (SCADA/PLC). MES sits in the middle of that tech stack, but its value is most visible where it directly supports execution: the moment a job hits the floor, operators receive instructions, machines begin producing, and data starts flowing.
This article focuses on the features that power real-time execution — the ones that coordinate people, machines, and materials in motion. These capabilities often represent the day-to-day touchpoints of MES: dispatching work orders, guiding operators through complex tasks, capturing live production status, and surfacing performance feedback instantly.
Why does this matter? Because most manufacturing problems — missed deadlines, quality escapes, unplanned downtime — aren’t caused by bad plans. They’re caused by poor execution, slow feedback, and decisions made with outdated or incomplete information. MES execution tools are designed to close that gap. They reduce delays, minimize errors, and empower frontline teams with the right information at the right time.
In the sections that follow, we’ll break down four core MES features that bring real-time execution to life on the shop floor — and offer practical insights into how they work, where they succeed, and how to deploy them effectively.
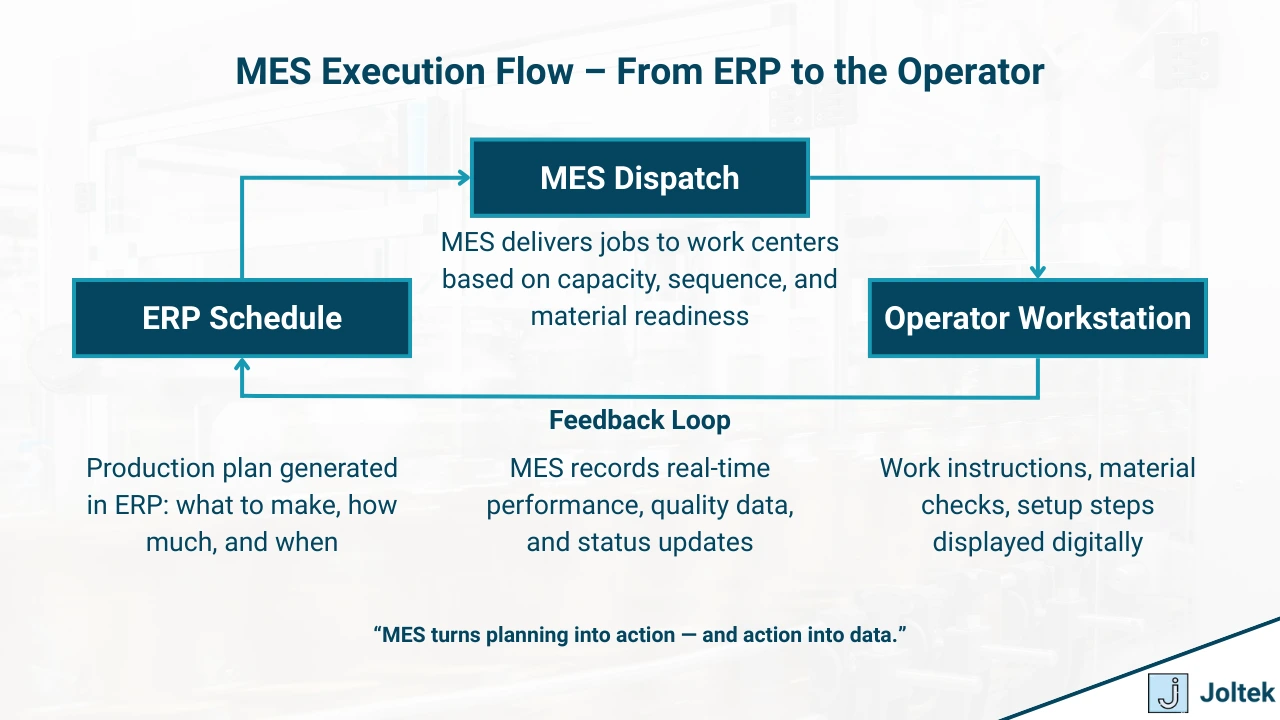
Real-Time Production Monitoring
What It Is
Real-time production monitoring is one of the foundational features of any MES system. It involves capturing live data from machines and work centers to provide immediate visibility into what’s happening on the factory floor. This includes knowing which equipment is running, how many units have been produced, current cycle times, and whether the process is operating within expected parameters.
This isn't just about passively recording output — it's about seeing the heartbeat of your production in the moment it happens.
How It Works
To achieve this, MES systems tap into multiple sources of plant floor data:
- SCADA systems and PLCs: These provide automated, high-frequency data such as machine state (running, idle, faulted), part counts, and cycle times. MES systems often connect to SCADA or directly to PLCs via industrial protocols (e.g., OPC UA, Modbus, Ethernet/IP).
- Sensors and I/O modules: Data from sensors — such as part presence, machine load, or torque — can offer additional context.
- Operator inputs: MES may also include digital forms or HMIs where operators log information manually (e.g., downtime reasons, quality flags, job completions).
This data is then structured and contextualized within the MES to create meaningful outputs:
- Dashboards showing current state by line, cell, or plant
- Alerts when performance drops below thresholds or faults occur
- Trend analysis for cycle time deviations, part rejection rates, or equipment reliability
Operational Impact
With real-time visibility, manufacturers can act before small problems turn into big ones. Examples of impact include:
- Faster problem detection: A spike in cycle time or a sudden drop in output triggers immediate investigation
- Improved OEE (Overall Equipment Effectiveness): More accurate downtime tracking and root cause analysis help improve availability and performance
- Better shift handovers: Teams coming on shift can see the current status, what’s running, what’s down, and what needs attention — without relying on whiteboards or verbal updates
Real-time monitoring also serves as the foundation for tiered daily management and performance huddles, turning MES data into a shared language across departments.
Common Challenges
Despite its value, many MES implementations fall short here due to:
- Incomplete data capture: Not all machines are connected, or only a subset of events (e.g., start/stop) are tracked
- Over-reliance on manual entry: Without automation, operator-entered data can be delayed, inconsistent, or inaccurate — reducing trust in the system
For real-time monitoring to be effective, connectivity must be prioritized, and context must be layered onto the raw data. Otherwise, it becomes just another screen with numbers — rather than a tool that drives action.
Work Order Dispatching and Execution Control
What It Is
Work order dispatching is where MES truly begins to operationalize the production schedule. While ERP systems determine what needs to be produced and when, it’s MES that turns those plans into reality on the shop floor. This feature ensures that the right jobs are sent to the right machines or operators, with the correct instructions, materials, and priorities — all in real time.
At its best, MES becomes the single source of truth for shop floor execution, eliminating guesswork and manual coordination.
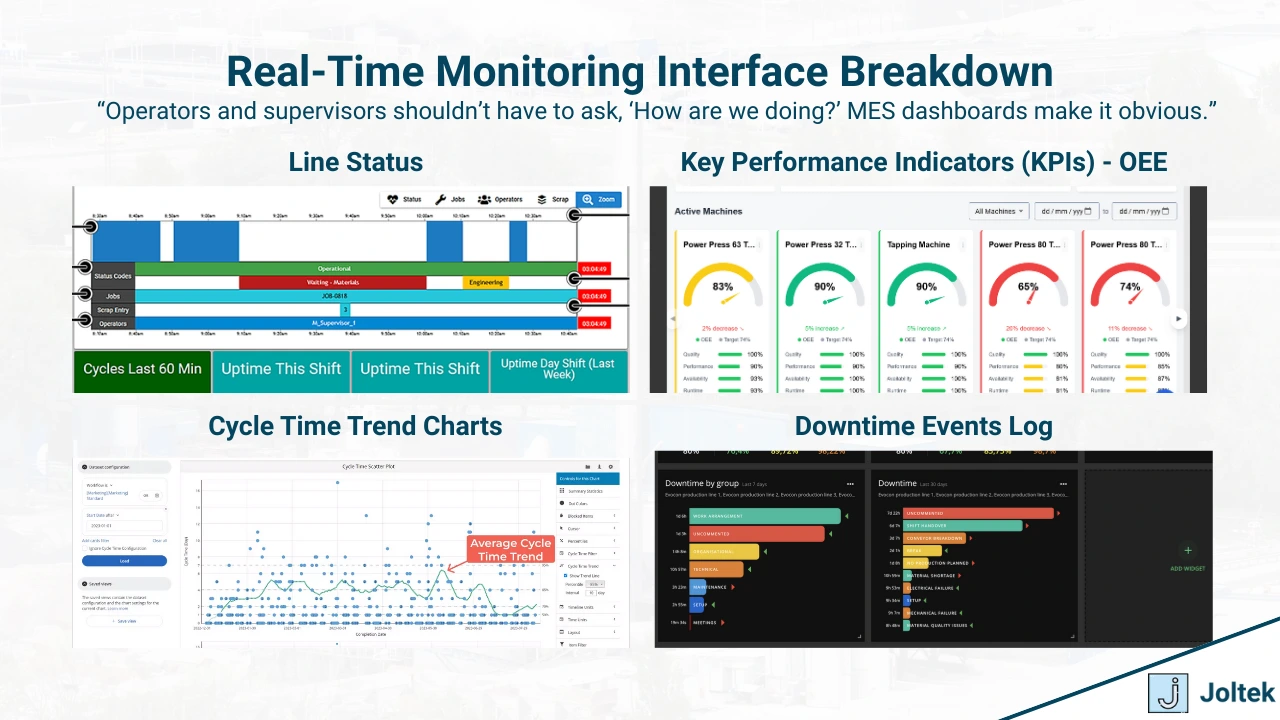
How It Works
MES systems ingest scheduled work orders from the ERP layer, then apply plant-specific logic to route them where they need to go. This process includes:
- Routing and Assignment: Jobs are assigned based on predefined production rules — by machine capability, resource availability, or operator certification.
- Digital Instructions: Operators receive job information at their stations, including part numbers, batch quantities, setup steps, tooling requirements, and inspection checkpoints.
- Sequencing Logic: MES can dynamically reorder jobs based on changes in demand, equipment availability, or rush orders.
- Material Checks and Pre-Conditions: Before a job begins, MES may validate material availability, ensure the correct recipe is loaded, and confirm that required tools or fixtures are present.
- Approval and Acknowledgment Steps: Some workflows require supervisor sign-off, digital sign-ins, or confirmation that pre-start tasks are complete before execution begins.
This entire process replaces paper travelers, dry-erase boards, and tribal knowledge with a structured, traceable digital workflow.
Operational Impact
The benefits of MES-based dispatching are felt almost immediately in complex environments:
- Reduces paperwork and confusion: Operators don’t need to hunt down instructions or verify priorities — it’s all presented digitally.
- Standardizes workflows: By enforcing sequence, materials, and process steps, MES ensures consistent execution across shifts and personnel.
- Supports high-mix, low-volume operations: In facilities with frequent changeovers and product variation, MES can adjust in real time, reducing the burden on supervisors and planners.
- Improves traceability and compliance: Digital execution logs ensure that every job has a timestamped record of who did what, when, and how — critical for audits or root cause analysis.
Common Pitfalls
Despite its clear benefits, this MES feature is often underutilized or implemented poorly due to:
- Unstructured or outdated master data: If product routings, BOMs, or job steps in the ERP system are inaccurate, MES execution will be flawed from the start.
- Manual overrides and workarounds: Operators may skip or bypass MES instructions if the system is slow, difficult to use, or doesn't reflect reality on the floor.
- Lack of integration with scheduling systems: If MES isn’t tightly connected to ERP or advanced planning tools, dispatching decisions may be out of sync with demand or constraints.
To succeed with MES dispatching, companies must invest in clean data, integration, and frontline buy-in. Otherwise, MES risks becoming another layer of digital overhead instead of a tool that actually helps people get work done.
Electronic Work Instructions and Operator Guidance
What It Is
Electronic Work Instructions (EWIs) are one of the most tangible ways MES improves how frontline teams interact with production. Instead of relying on printed binders, static PDFs, or verbal guidance, MES delivers digital instructions to operators — tailored to the product, workstation, or job in progress.
These can include step-by-step directions, visual aids, checklists, tool references, safety warnings, and inspection requirements — all presented contextually and in real time.
How It Works
As soon as a work order is dispatched, MES surfaces the correct instructions based on:
- Part number, recipe, or product variant
- Work center or operation step
- Version-controlled documents tied to the routing or BOM
Instructions are displayed on terminals, tablets, HMIs, or smart displays directly at the point of use. In more advanced deployments:
- Interactive forms collect operator confirmations or checklists
- Embedded media such as images or short videos guide complex assembly steps
- Conditional logic adjusts instructions based on quality results, material types, or job status
MES may also prompt for digital sign-offs, approvals, or alerts if steps are skipped or performed out of order.
Operational Impact
For facilities with high variability or regulatory complexity, EWIs offer major benefits:
- Faster onboarding and cross-training: New or rotated operators can follow guided steps without tribal knowledge or constant supervisor support.
- Reduced errors and rework: Visual instructions and embedded verifications ensure critical steps aren’t missed or misinterpreted.
- Consistency across shifts and sites: Standardized instructions enforce best practices and compliance — critical in medical, aerospace, automotive, and food industries.
- Traceability for audits: Digital signatures and execution records prove that each step was followed as designed.
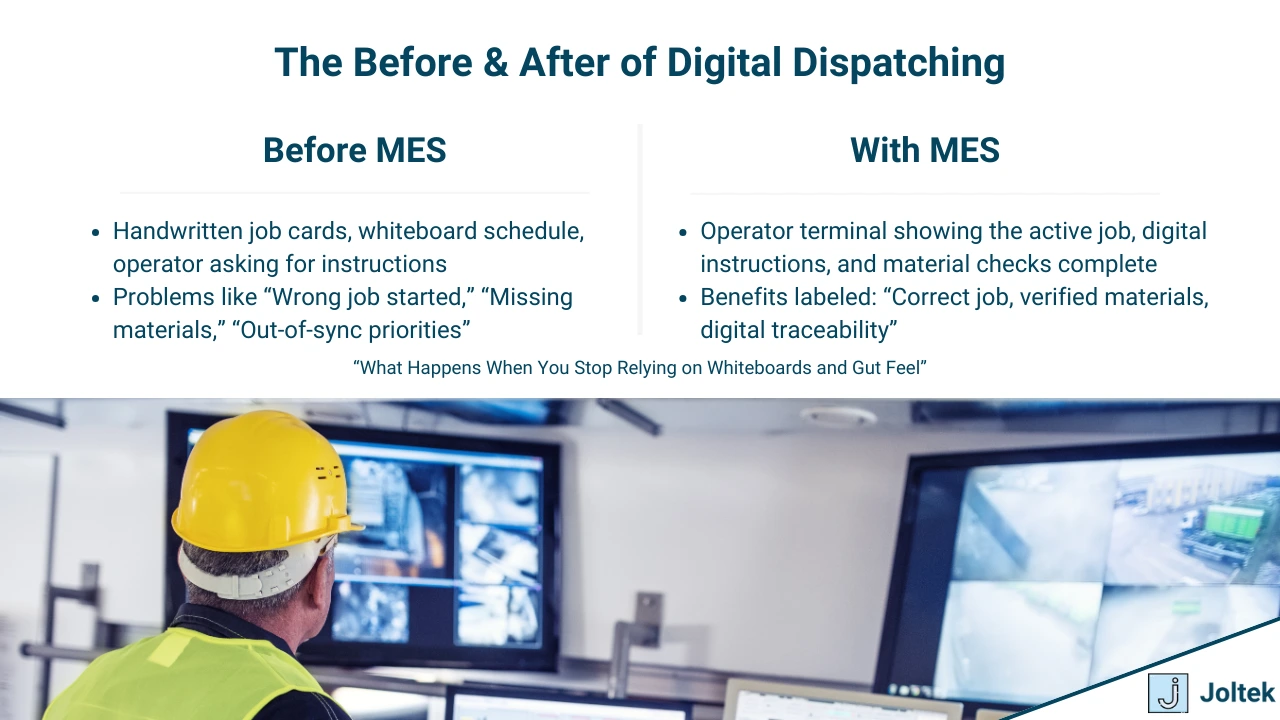
Implementation Tips
To get the most out of EWIs:
- Involve operators in development: They know where legacy instructions are unclear or outdated.
- Start with high-mix or high-defect processes: These see the fastest ROI from standardized, visual guidance.
- Integrate with quality checkpoints: Embed sign-offs and inspection prompts to ensure compliance as part of the workflow — not after the fact.
Dashboards and KPIs for Frontline Teams
Dashboards are where MES systems translate raw production data into real-time feedback that frontline teams can actually use. While performance metrics like OEE, scrap rate, and cycle time are often reviewed at the management level, the real value comes when those insights are made visible, actionable, and timely for the people closest to the process.
At their core, MES dashboards provide a live snapshot of how production is performing — not just by shift or day, but by the minute. They display line status, counts, downtime, quality trends, and operator performance in formats tailored to each user. These dashboards are typically mounted on overhead displays in production areas, accessed via terminals at workstations, or even pushed to mobile devices for supervisors and team leads.
The purpose isn’t just to report numbers. A good MES dashboard creates alignment across roles: operators understand whether they’re ahead or behind; maintenance sees when lines are trending toward failure; and managers can identify where to focus their attention. It turns abstract KPIs into something tangible that drives real-time decision-making. For example, a visual OEE breakdown can help an operator understand that while the line is running at target speed, their changeovers are causing frequent small stops — something they can begin addressing that very shift.
However, many dashboards fail to move the needle because they’re either too complicated, too generic, or disconnected from what operators actually influence. A screen full of charts is not helpful if it doesn’t tell the user what to do. The most effective implementations focus on simplicity, relevance, and timing. Rather than showing 15 metrics, they show the 3 that matter most in that context — with clear indicators for what’s good, what’s at risk, and what requires action.
When designed well, real-time dashboards do more than monitor performance — they create a culture of ownership. They reinforce daily goals, highlight issues while they’re still small, and empower teams to solve problems without waiting for a morning meeting or an end-of-day report.
Conclusion: Real-Time Execution Is Where MES Delivers Its Value
For all the talk of digital transformation and smart manufacturing, success on the factory floor still comes down to execution. Can your team respond to issues in real time? Are the right jobs running with the right materials? Do operators have the information they need — when and where they need it?
This is where MES proves its worth. Features like real-time production monitoring, digital work order dispatching, operator guidance, and actionable dashboards aren't just software modules — they’re tools that close the gap between planning and reality. They bring structure to daily operations, visibility to performance, and consistency to complex processes.
Yet, these tools only create value if they’re used intentionally. Without clean data, good integration, and frontline buy-in, MES can quickly become just another screen on the wall. But when implemented thoughtfully, it becomes the system your teams rely on to get work done — faster, better, and with fewer surprises.
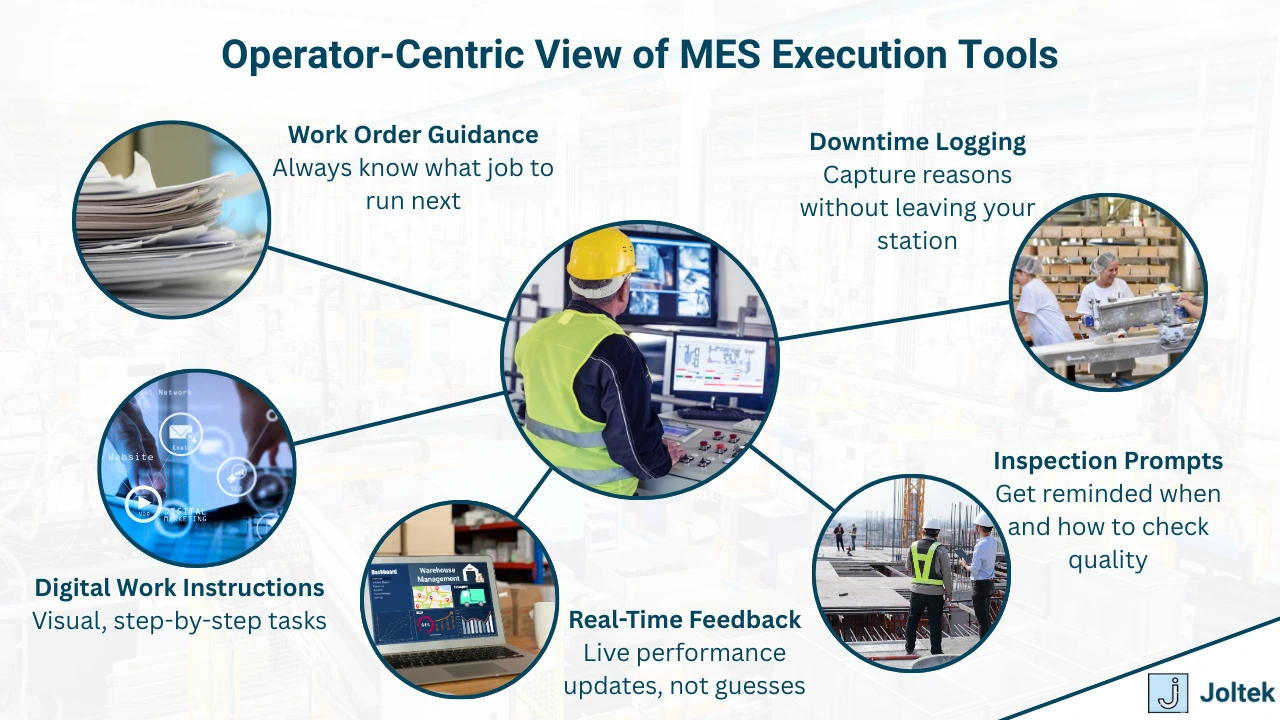
In the next article of this series, we’ll continue to explore how other MES features — like quality management, traceability, and downtime analysis — help build a foundation for continuous improvement and compliance. Until then, take a moment to walk your floor and ask: Is MES truly driving execution here? Or just tracking it after the fact?
If the answer is unclear, it may be time for a deeper look.