Introduction: Why Quality and Traceability Are Non-Negotiable
In today’s manufacturing environment, quality failures aren’t just costly — they’re business-critical. A single recall can result in lost contracts, regulatory scrutiny, brand damage, or worse. In regulated industries like pharmaceuticals, medical devices, or food and beverage, even a minor compliance gap can trigger audits, fines, or product holds. But even outside those sectors, customers expect consistency, traceability, and confidence in every unit that leaves your facility.
That’s why quality and traceability aren’t just the responsibility of the quality department — they’re fundamental to your production system. And this is where MES proves its deeper value.
A well-implemented MES doesn’t wait for problems to surface after production. It catches them early, enforces standards as work is being done, and creates a digital trail of every action, inspection, and deviation. It connects quality checks directly to execution, ensures traceability at every step, and provides the documentation required to pass audits and resolve customer complaints with confidence.
This article explores the core MES features that support high-integrity manufacturing — from in-process quality control and product genealogy, to non-conformance management and electronic records. Whether your facility is in a regulated space or not, the ability to build traceable, reliable processes at scale is no longer optional — it’s a competitive necessity.
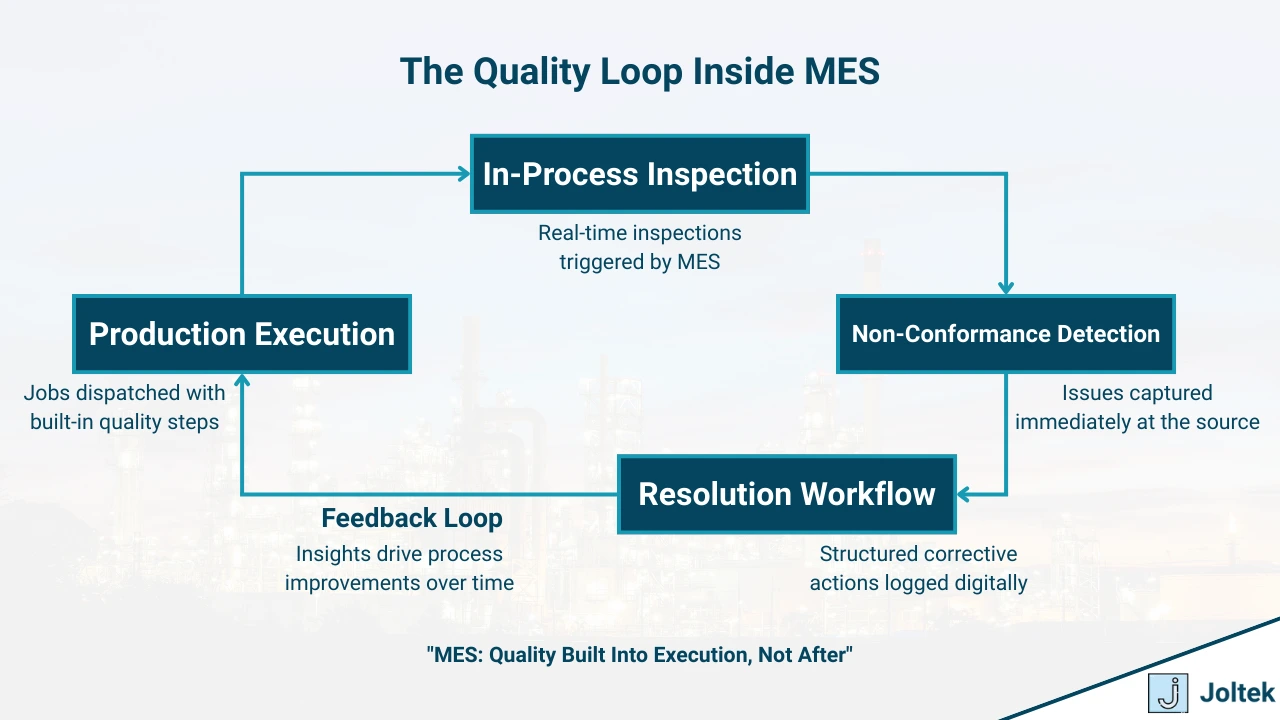
In-Process Quality Control and SPC Integration
What It Is
In-process quality control is one of the most powerful — yet often underutilized — capabilities of an MES. Rather than relying solely on end-of-line inspections to catch defects, MES embeds quality checks directly into production workflows. It ensures that inspections happen at the right time, on the right product, by the right person, with immediate capture of results.
When paired with Statistical Process Control (SPC) tools, MES doesn't just detect defects — it monitors trends in real time to catch process variations before they result in scrap or rework.
How It Works
As a job progresses through the production line, MES prompts operators or automated systems to perform specific inspections based on part numbers, lot numbers, or process steps. This could include dimensional checks, visual inspections, torque measurements, or even inline sensor readings.
Each inspection point is digitally logged in the MES:
- Pass/fail results, measured values, and defect types are recorded
Results can trigger immediate alerts if out-of-spec conditions are detected - Data feeds SPC systems, enabling real-time control charting, trend analysis, and early warnings for process drift
More advanced MES systems allow dynamic sampling plans — increasing inspection frequency when issues are detected, or tightening tolerances for critical lots.
Operational Impact
The operational impact of integrating in-process quality control into MES is significant. Problems are caught at the source, not downstream after value has been added. Scrap and rework are minimized, shift-to-shift variability is reduced, and customers experience fewer defects.
For regulated industries, this digital traceability is not just a best practice — it’s often a regulatory requirement. Automated prompts, required data entry, and locked workflows ensure that inspections aren’t skipped or completed out of sequence.
Beyond compliance, early detection leads to more stable processes, higher first-pass yields, and stronger continuous improvement efforts — because now you have the data to see where and when variation creeps in.
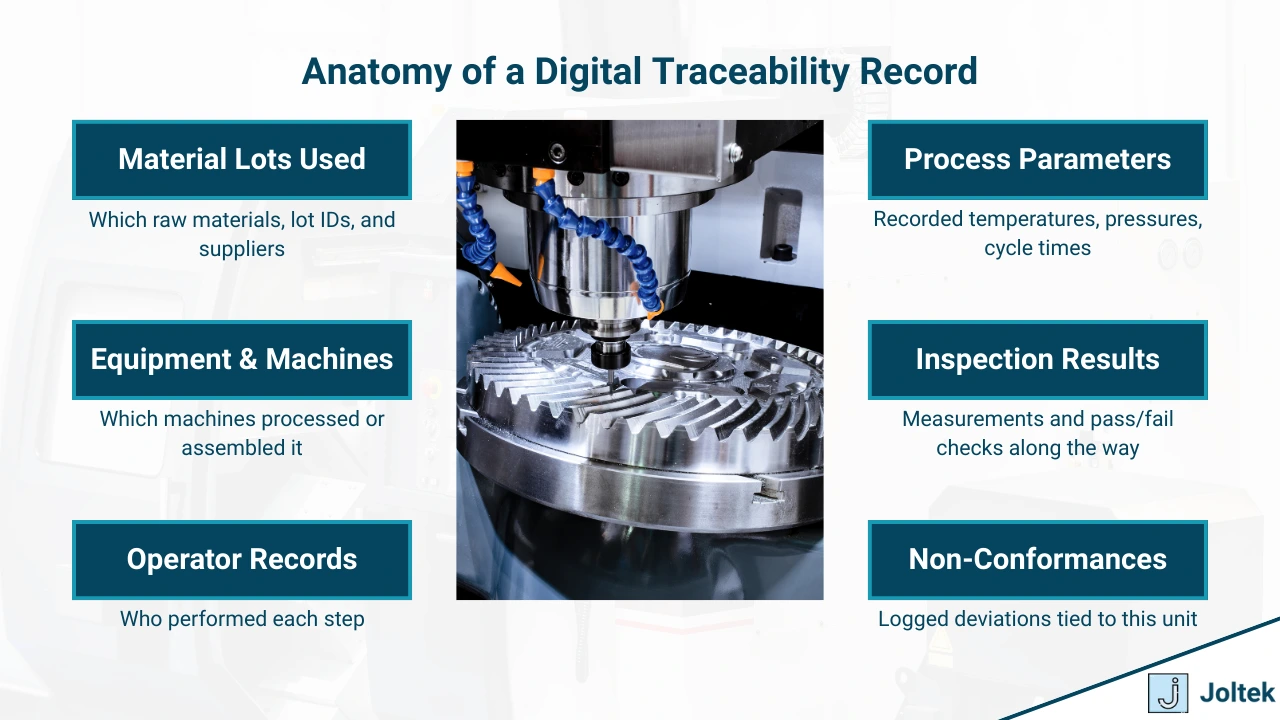
Traceability and Product Genealogy
What It Is
Traceability is the ability to track every product, lot, or batch throughout its entire production lifecycle — from raw materials and components, through processing, assembly, and final shipment. Product genealogy takes this a step further, creating a detailed digital history of everything that touched or influenced that product along the way: materials, machines, operators, process parameters, inspections, and environmental conditions.
In today’s manufacturing landscape, traceability is no longer a “nice-to-have” — it’s essential for regulatory compliance, customer trust, and operational risk management.
How It Works
MES captures traceability data automatically as work is executed on the shop floor. As each unit moves through its route:
- Raw material lot numbers are linked to the finished product
- Machine IDs and operator badges are logged at each workstation
- Key process parameters (such as temperature, torque, cycle time) are recorded
- In-process inspection results and non-conformance events are tied to specific parts or batches
This information forms a complete, structured genealogy that can be queried instantly. If a defect is detected, a single click can reveal which batch it came from, what materials were used, what equipment was involved, and what process conditions existed at each step.
In more advanced implementations, MES integrates with ERP and warehouse systems to extend traceability upstream (to suppliers) and downstream (to customers).
Operational Impact
The benefits of real-time, digital traceability are immediate and far-reaching.
In the event of a quality issue, manufacturers can isolate affected lots in hours instead of days — reducing recall costs, protecting brand reputation, and minimizing disruption. Instead of pulling all units from a month’s production, you can surgically target only the products at risk.
Even without a crisis, traceability provides everyday operational value. It supports warranty claims, strengthens supplier accountability, improves root cause analysis, and satisfies even the most demanding customer or regulatory audits.
For manufacturers in industries like automotive, aerospace, electronics, and pharmaceuticals, the absence of robust traceability is not just a vulnerability — it’s a potential showstopper. MES makes traceability a byproduct of execution, not an afterthought.
Non-Conformance Management and Exception Handling
What It Is
Even in the best-run factories, deviations from standard processes happen. Materials fall out of spec, equipment drifts, operators encounter unexpected conditions. Non-conformance management is the MES capability that brings structure to how these deviations are identified, recorded, escalated, and resolved.
Rather than relying on paper forms, ad-hoc emails, or delayed reporting, MES builds non-conformance detection and handling directly into the production workflow — ensuring that every issue is captured immediately and managed systematically.
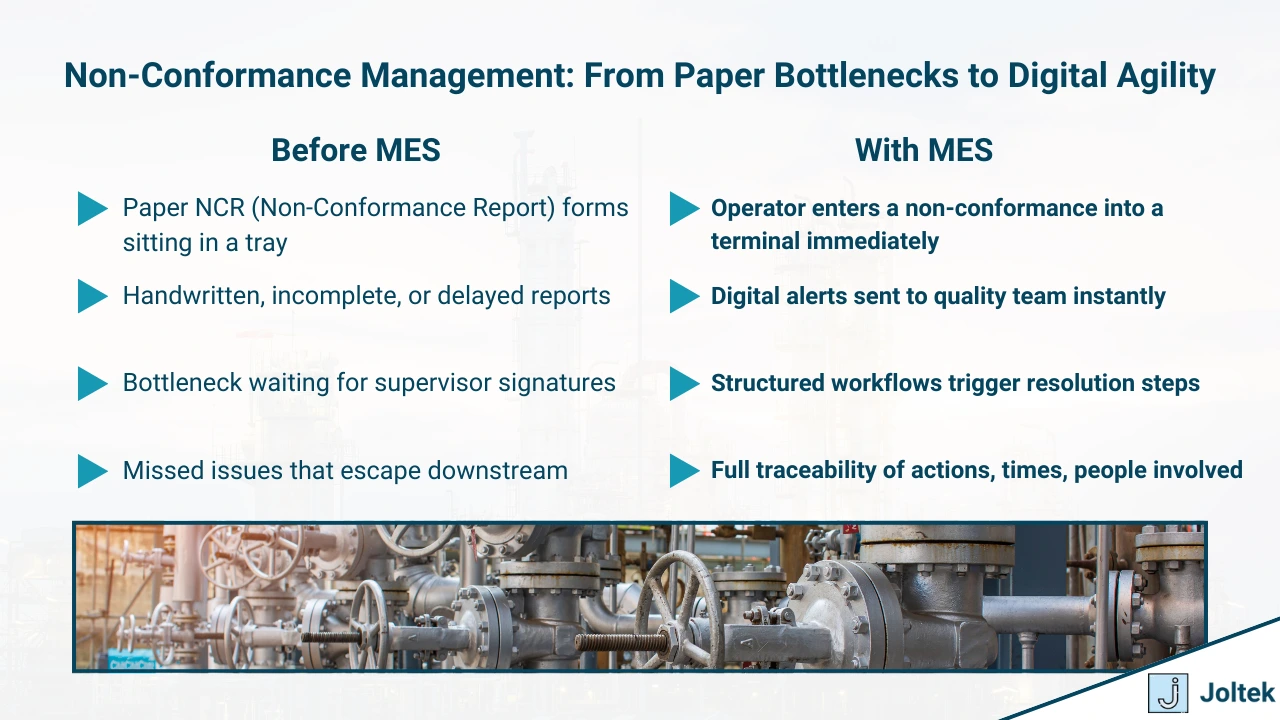
How It Works
When a defect is detected or a process condition falls outside of acceptable limits, MES can automatically or manually trigger a non-conformance event. The system captures:
- The nature of the issue (e.g., out-of-spec measurement, failed inspection, missing material)
- The part, lot, or work order affected
- The responsible station, machine, or operator
- Time and context of the event
MES can then enforce preconfigured workflows, such as:
- Requiring supervisor review before proceeding
- Locking downstream processes until disposition is decided (e.g., rework, scrap, quarantine)
- Escalating high-severity issues to quality or engineering teams
- Linking corrective actions, re-inspections, or deviation approvals
All actions are digitally logged with timestamps, user IDs, and audit trails, ensuring full traceability for future analysis or compliance needs.
Operational Impact
The operational benefits of embedding non-conformance management into MES are significant.
First, it ensures that no issue slips through the cracks. Problems are addressed at the source, before they flow downstream into larger batches, final products, or — worse — customer shipments. This reduces the cost of poor quality (COPQ), protects brand reputation, and accelerates root cause resolution.
Second, structured non-conformance data becomes a powerful tool for continuous improvement. Patterns emerge: recurring material defects from a supplier, repeated operator errors at a certain station, specific machines that trend toward failures. Instead of reacting to problems, manufacturers can proactively eliminate their root causes.
Finally, in highly regulated industries, electronic non-conformance records are essential for demonstrating compliance with standards such as ISO 9001, AS9100, or GMP guidelines. MES ensures that every deviation is documented, traceable, and part of a closed-loop quality system.
Audit Trails and Electronic Signatures
What It Is
In industries where compliance is non-negotiable, proving that the right actions were taken — by the right people, at the right time — is just as important as the actions themselves. Audit trails and electronic signatures are MES capabilities designed to create that proof automatically. They provide a secure, unalterable record of every interaction with the system, turning execution into defensible evidence for regulators, auditors, customers, and internal stakeholders.
Electronic signatures go a step further, enabling authenticated digital approvals that meet strict regulatory standards like FDA 21 CFR Part 11 for pharmaceuticals and medical devices.
How It Works
Every meaningful action performed through MES — whether it’s starting a job, completing a quality inspection, logging a non-conformance, or changing a recipe — is automatically recorded with:
- Who performed the action (linked to a user account or operator badge)
- What action was taken
- When it occurred (with an exact timestamp)
- Where it happened (station, machine, device)
For critical actions, the system may require an electronic signature — a digital credential (password, badge scan, biometric input) confirming the identity of the person performing or approving the step. In regulated environments, electronic signatures are often paired with a reason for change or action, adding further context to the record.
All of this information is stored securely and made easily searchable, creating a complete and tamper-evident execution history.
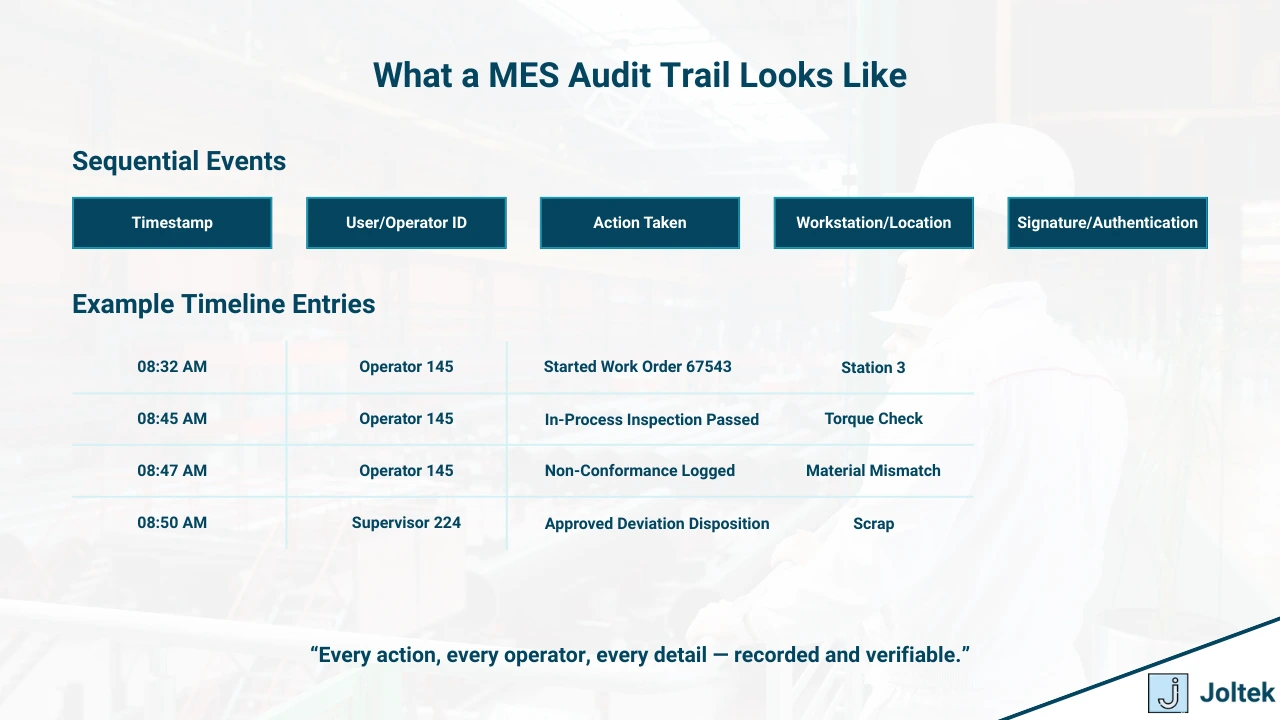
Operational Impact
Robust audit trails and electronic signatures transform compliance from a painful, manual exercise into a built-in strength.
Instead of scrambling to reconstruct actions during audits or investigations, manufacturers with strong MES records can simply pull verified reports — demonstrating not only what happened, but also who authorized it and why. This greatly reduces audit preparation time, avoids costly documentation errors, and increases confidence during inspections.
Moreover, audit trails aren't just for regulators. They help internal teams quickly investigate issues, understand workflows, and improve processes. Having transparent, trusted execution data supports faster root cause analysis, better training, and stronger operational discipline.
In a world where supply chains are under scrutiny and regulatory standards are rising, MES audit trails and electronic signatures aren’t just about compliance — they’re about building operational resilience and customer trust.
Conclusion: MES as the Digital Backbone of Quality
In manufacturing, quality is no longer a department — it’s a system. It's a set of practices and controls that must be embedded into every step of production, from material receipt to final shipment. Manufacturing Execution Systems (MES) provide the digital backbone that makes this possible.
By integrating quality checks into daily operations, enforcing real-time traceability, structuring non-conformance handling, and maintaining bulletproof audit trails, MES transforms quality from a reactive exercise into a proactive, continuous process. It ensures that problems are caught early, deviations are documented and resolved systematically, and every product carries with it a verifiable, trustworthy history.
For manufacturers competing in regulated industries, MES isn't optional — it's a necessity for survival. But even outside strict compliance environments, the ability to detect issues early, prove process integrity, and build traceability into the flow of work is a powerful competitive advantage.
As you look at your own operations, ask yourself: is your quality system truly integrated with your production processes? Or is it still riding alongside, disconnected and delayed?
In future articles, we’ll continue exploring how MES supports broader manufacturing excellence — from downtime reduction to inventory control and production scheduling. But wherever you are in your journey, remember this: building a culture of quality starts with building a system that enforces and elevates it. MES is that system.