Introduction: Why MES Deserves a Closer Look
Manufacturing Execution Systems (MES) have long sat at the intersection of enterprise planning and shop floor operations — often underappreciated, frequently misunderstood, but critically important. Positioned between ERP systems and real-time control systems like SCADA and PLCs, MES acts as the digital nerve center of the factory, coordinating workflows, tracking performance, and enforcing process standards.
Yet despite its pivotal role, MES is frequently reduced to a narrow stereotype: “production tracking software.” In many organizations, it’s seen as a digital clipboard that logs output counts and downtimes — helpful, but not strategic. That perception undersells the real value of a well-implemented MES.
In reality, MES is one of the few systems in a manufacturing environment that touches people, processes, equipment, and data all at once. When properly configured and integrated, it enables:
- Real-time visibility into what's happening on the shop floor
- Seamless traceability for every unit or lot produced
- Standardized execution of production processes
- Faster feedback loops for addressing quality or downtime issues
- And a growing role in digital transformation efforts
In an era where supply chain pressures are relentless, skilled labor is in short supply, and customer demands are rising — the need for responsive, data-driven manufacturing has never been higher. That’s exactly where MES shines.
This article kicks off a new series aimed at unpacking the most utilized MES features, how they work, and how manufacturers are leveraging them for better performance and control. Whether you’re evaluating MES for the first time or looking to get more from your current implementation, understanding the fundamentals is the first step.
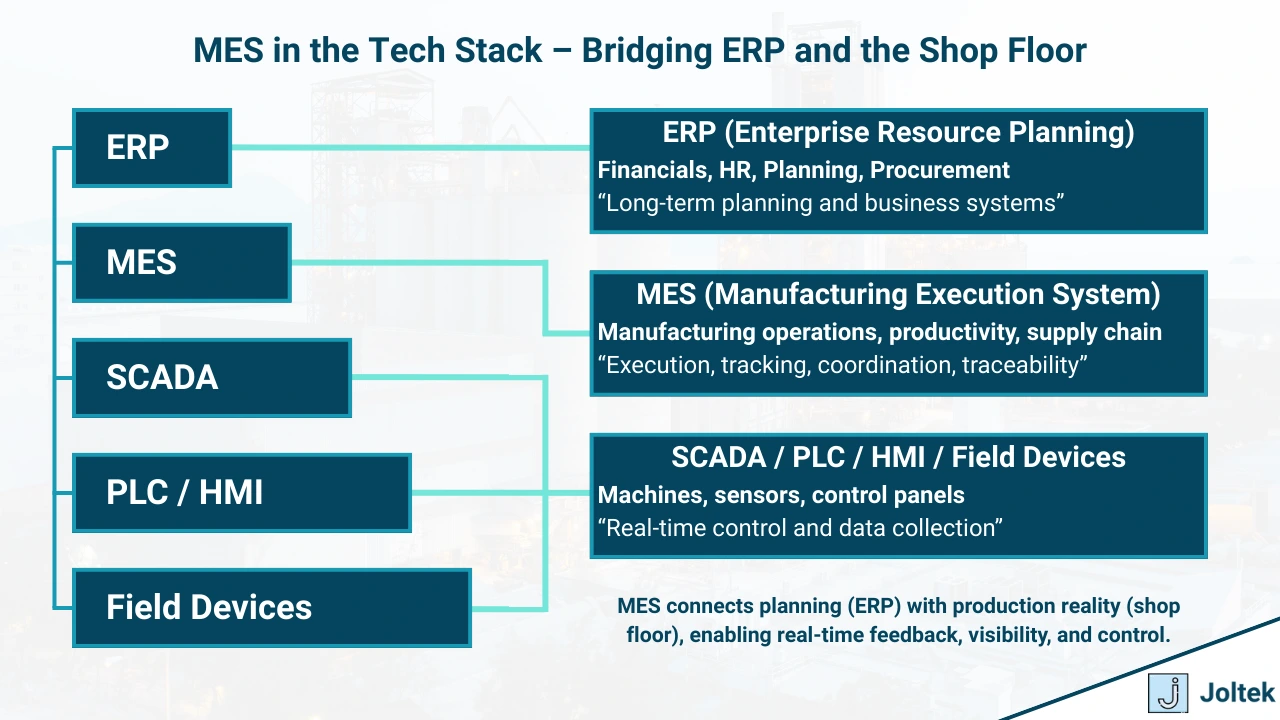
What Is MES Really Doing on the Plant Floor?
At its core, a Manufacturing Execution System (MES) is about coordination — making sure the right people, machines, materials, and instructions are aligned in real time to execute production effectively.
If you walk onto a factory floor without MES, you’ll often find siloed systems, paper travelers, verbal instructions, and a reactive firefighting culture. With MES, the entire environment becomes connected: job priorities flow from ERP, machines feed back live production data, operators get digital instructions, and supervisors have dashboards showing how each line is performing.
To understand MES's impact, it helps to group its value into three key categories:
1. Visibility
MES provides a real-time window into operations. It tells you:
- What’s running right now?
- Is the line up or down?
- How many units have we produced?
- Are we on schedule?
This visibility is foundational. Without it, decision-makers are left relying on delayed reports, gut feel, or walking the floor for answers. With MES, production status is available on screens across the factory — or remotely, if needed — giving teams the ability to respond faster and more confidently.
2. Control
MES standardizes execution. It ensures that:
- Operators follow the right work instructions
- Machines run with the correct parameters and recipes
- Quality checks happen at the right time and place
- Jobs flow in the correct sequence
This level of control reduces variability, speeds up changeovers, and supports compliance with internal or external standards (like GMP, ISO, or customer audits). MES doesn’t just show you what's happening — it helps ensure that what should happen is actually happening.
3. Improvement
MES enables continuous improvement by generating high-quality data:
- Downtime reasons and frequencies
- Quality defect trends
- OEE components (availability, performance, quality)
- Material usage vs. plan
With this data, manufacturers can prioritize improvements based on facts, not assumptions. Whether it’s reducing scrap, optimizing line speed, or fine-tuning maintenance strategies, MES provides the feedback loop needed for operational excellence.
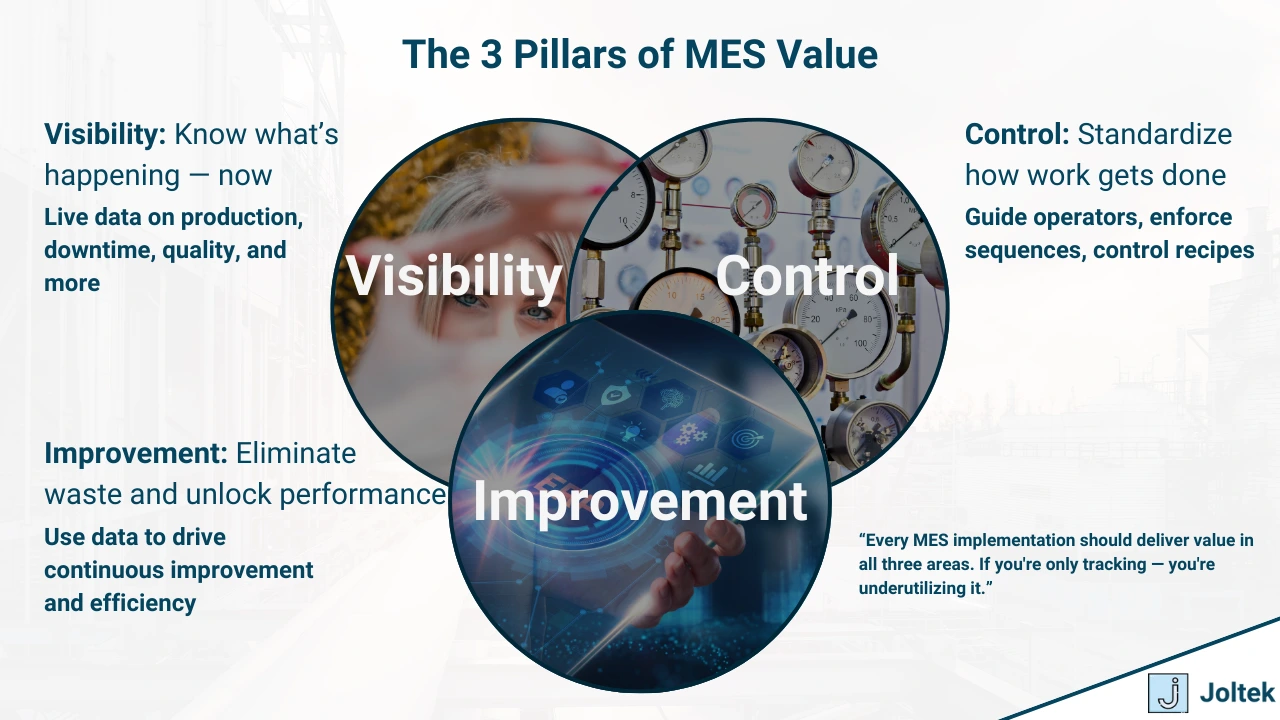
The Most Utilized MES Features
The power of MES lies in its ability to connect the shop floor with real-time data and structured workflows. Below are the most commonly used MES features — not just in name, but in how they actually support operations, quality, and strategic decision-making.
Real-Time Production Monitoring
An MES collects data from machines, sensors, and operator inputs to provide a live view of what’s happening on the floor. Production counts, cycle times, run states, and even scrap quantities are tracked and displayed in real time. This allows supervisors and planners to identify bottlenecks, track actual vs. planned performance, and make adjustments before small issues escalate into major downtime.
Work Order Dispatching
Rather than relying on paper travelers or manual communication, MES systems electronically deliver work orders to stations or operators. These instructions include which job to run, which components to use, what tooling is needed, and which steps to follow. This reduces errors, speeds up job transitions, and helps ensure production is aligned with schedule priorities and material availability.
Quality and SPC Tools
Quality control is embedded directly into the production process. MES can prompt operators to perform inspections at predefined intervals or conditions, enforce pass/fail criteria, and collect quality data for real-time SPC (Statistical Process Control). Alerts can be triggered if trends fall outside of control limits, allowing teams to address issues before they impact product quality at scale.
Traceability
Traceability is one of the most critical capabilities for regulated industries like food & beverage, pharmaceuticals, and automotive. MES tracks every unit or batch as it moves through production, logging which raw materials were used, which equipment and operators were involved, and what parameters were applied. In the event of a defect or recall, this granular traceability enables fast, focused root cause analysis and corrective actions.
Downtime Tracking
Every stop on the line has a cost — and MES helps capture those events automatically or via operator input. Systems can classify downtime reasons (e.g., mechanical failure, waiting on materials, changeover) and track frequency and duration. This data supports maintenance planning, continuous improvement efforts, and even justifying capital investments in automation or reliability upgrades.
Dashboards and KPIs
MES dashboards surface real-time performance data across roles — from operators and team leads to plant managers and corporate leadership. Common KPIs include OEE (Overall Equipment Effectiveness), first-pass yield, scrap rate, and throughput. By making these metrics visible and timely, MES drives accountability and empowers faster, more informed decisions.
Recipe and Parameter Management
For process manufacturing and mixed-model production, MES stores and enforces product-specific settings — such as temperature, speed, pressure, and other key parameters. These recipes can be downloaded directly to machines or validated by operators before the job starts. The result: consistent output, fewer deviations, and faster setup times across SKUs.
Inventory and Material Tracking
MES systems track material consumption in real time, updating WIP status and flagging when materials are low or missing. By integrating with barcode scanners, RFID, or vision systems, MES helps ensure accurate part usage and location tracking — reducing overstock, shrinkage, and manual data entry errors. This is especially important in just-in-time or lean environments where inventory visibility is critical.
.webp)
Why These Features Matter
MES is not just a layer of software — it's an engine for operational excellence. In a modern manufacturing environment, where complexity is rising and margins are tightening, MES provides the structure and visibility needed to stay competitive.
When properly configured and adopted, MES becomes a catalyst for:
- Lean manufacturing: by identifying waste in the form of downtime, excess inventory, rework, or inefficient workflows.
- Standardized execution: ensuring that processes are followed consistently across shifts, operators, and equipment.
- Faster decision-making: with real-time data available at every level — from operator to plant manager — problems can be addressed before they cascade.
- Digital transformation: as a central piece of the IT/OT stack, MES helps manufacturers digitize core processes, unlock contextualized data, and lay the groundwork for advanced analytics, AI, or predictive systems.
The result? Measurable performance gains. Many manufacturers using MES see:
- Reduced scrap and rework through early detection of process variation
- Improved OEE via better downtime categorization and targeted improvements
- Shorter lead times and faster response to changing demand or production issues
- Fewer surprises thanks to real-time visibility into material flow, job status, and quality
Case-in-Brief
A mid-sized medical device manufacturer struggled with frequent, unexplained downtime across multiple lines. By implementing a basic MES module focused on real-time machine status and downtime reason tracking, the team discovered that 42% of stops were due to a single recurring issue — unplanned changeovers triggered by missing materials. After adjusting inventory staging processes and enforcing digital work order sequencing through MES, they reduced unplanned downtime by 28% within three months.
Common Pitfalls and Missed Opportunities
Despite its potential, MES doesn't always deliver transformational results — and in many cases, the issue isn’t the software itself. It's how it's implemented, integrated, or adopted. These are some of the most common ways MES falls short:
“Glorified Data Logger” Syndrome
One of the biggest issues is treating MES as little more than a passive data collection tool. Systems are installed to record downtime, production counts, and quality metrics — but the data isn’t used to drive action. Without structured workflows, alerts, or frontline engagement, MES becomes a glorified clipboard rather than a system for execution. It collects noise instead of generating insight.
Poor Integration with ERP, CMMS, or SCADA
MES can’t operate in a vacuum. When it doesn’t integrate cleanly with upstream systems like ERP (for scheduling, inventory) or downstream systems like SCADA (for real-time machine data), its effectiveness is limited. Gaps in integration lead to duplicated work, outdated information, and frustrated users — especially in environments with high product complexity or tight production timelines.
Lack of User Training and Change Management
Even the best MES system will fail if people don’t know how — or why — to use it. Operators, supervisors, and engineers must understand how the system supports their roles and what data matters. Without proper onboarding, systems are bypassed, data is entered inconsistently, and adoption suffers. Too often, companies underestimate the cultural shift MES requires and fail to include shop floor voices during implementation.
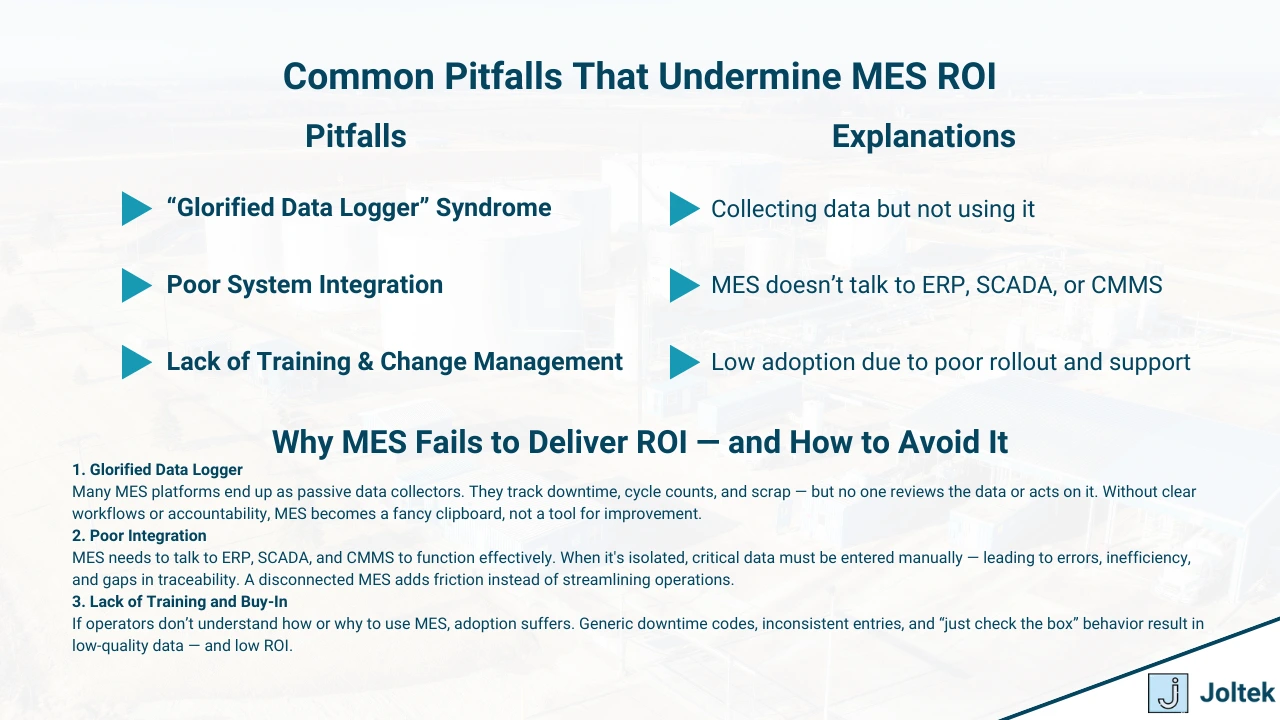
What’s Next in the Series
This article was just the beginning. Over the coming weeks, we’ll be taking a deeper dive into each of the core MES features outlined here — exploring how they work, where they deliver value, and how leading manufacturers are using them to drive real improvement.
Topics will include:
- Real-world use cases and implementation stories
- Technical considerations like integration and architecture
- Common challenges and how to overcome them
- Lessons learned from underperforming MES deployments
Whether you're just starting to explore MES or you’ve had one in place for years, this series is designed to help you get more out of your system — with clear insights you can apply directly to your facility.
Take a moment to reflect: Is your MES doing more than just tracking downtime?
- Are operators using it to guide their work?
- Are you capturing the data needed for real improvement?
- Are you acting on what your MES is telling you?
If the answer isn’t a confident “yes,” now is the time to take a closer look.
Call to Action
Want to benchmark your current MES setup or identify opportunities for better performance?
➡️ Subscribe to follow the rest of the series
➡️ Share this with a colleague who needs to see it
➡️ Or get in touch for a no-obligation MES audit or consultation — we’ll help you figure out what’s working, what’s not, and where to go next.